Карьерные роботизированные самосвалы
Роботизированные самосвалы, предназначенные для автономной работы на предприятиях по добыче природных ресурсов.
По мере совершенствования автопилотов для создания автономных транспортных средств, появляются все более совершенные решения роботизированных карьерных самосвалов и другой техники, которая может применяться при автономизации добычи полезных ископаемых. Подробнее о теме использования такой техники смотрите страницу «Добывающие компании и роботизация»
Каталог решений
КАМАЗ, КАМАЗ и ВИСТ Групп, Россия
В России также не первый год идет разработка карьерного роботизированного самосвала. Есть заказчик разработки — ОАО “Магнитогорский металлургический комбинат”. Разработкой системы самоуправления занимается “ВИСТ Групп”. Работы начались еще в 2016 году, но по состоянию на начало 2019 года о каком-то массовом использовании КАМАЗ-65801 или аналогичных карьерных грузовиков с самоуправлением, информации не поступало.
Проект разработки карьерного грузовика для ОАО ММК КАМАЗ-65801 с грузоподъемностью 45 тонн.
2016.10.11 КАМАЗ и ВИСТ Групп займутся карьерными роботизированными самосвалами для ММК. Создана рабочая группа для разработки беспилотной системы на базе самосвала КАМАЗ с ИИ в рамках выполнения заказа ОАО Магнитогорский металлургический комбинат. В нее вошли ПАО «КамАЗ», ОАО ММК и ОАО ВИСТ Групп. Будет разработан алгоритм управления и создана система диспетчеризации парком автомобилей-роботов. Рабочая группа пока что начнет с разработки ТЗ на создание самосвала-беспилотника для нужд ММК.
Caterpillar, США
В ноябре 2018 года компания Caterpillar сообщила, что ее карьерные самосвалы, оснащенные системой Cat Command, достигли рубежа в 1 млрд перевезенных тонн. Это также беспилотные самосвалы, которые самостоятельно реагируют на вызовы, поступающие от экскаваторjd, перемещаются в нужное положение, перевозят породу к месту разгрузки и предоставляют необходимую телеметрию, включая отчеты, необходимые для принятия решений о необходимости техобслуживания.
Caterpillar развернула свои первые шесть коммерческих автономных грузовиков в 2013 году, с тех пор парк роботизированных самосвалов компании вырос до более, чем 150 машин. Ими пользуются 6 различных горнодобывающих компаний в Австралии, Южной Америке и Северной Америке, например, на выработках компании Fortescue Metals Group. На март 2019 года в автопарк входят такие роботы, как Cat 793F. Cat 797F, Cat 789D, способные перевозить, соответственно 227 тонн, 363 тонны и 181 тонну.
Комментируя эту достижение, менеджер по продукции компании Caterpillar Mining Technology Шон МакГиннис сказал: “В процессе перевозки 1 млрд тонн автономные грузовики проехали почти 35 млн км без трав и потерь рабочего времени людей, в связи с автономными перевозками. Было наглядно показано, как можно повысить безопасность процессов, устранить ошибки эксплуатации самосвала и сократить число людей, работающих в районе активной добычи”.
Горнодобывающие компании по всему миру, особенно, в Чили, Австралии и Канаде, переходят от парка пилотируемых грузовиков к беспилотным роботам. Водителя в них замещает локальная система самоуправления и центральный контроллер. Для навигации автопилоты используют спутниковую навигацию GPS, также она используется для определения местоположения, скорости и направления движения других транспортных средств. Внедрение автономных перевозок означает для компании прямой рост производительности, поскольку больше материала может быть перемещено эффективно и безопасно.
Cat Command — это набор решений, от телеуправления до полностью автономных систем самоуправления. Система позволяет автономизировать не только перевозку породы, но также, например, работу бульдозеров.
Hitachi, Япония
Компания ведет разработку, но пока что не поставляет свои самосвалы на рынок.
Komatsu, Япония
Карьерные роботизированные самосвалы. Могут использоваться в телеуправляемом, полуавтономном и автономном режимах. Навигацию самосвалов обеспечивают модули GPS, радары и лазерные сенсоры.
Крупнейшие горнодобывающие корпорации все активнее внедряют беспилотные автопарки: это повышает безопасность и эффективность при перемещении больших объемов материалов. В ноябре 2018 года автономная система транспортировки (AHS) Komatsu Front Runner достигла важной вехи — беспилотные карьерные самосвалы компании переместили более 2 млрд тонн поверхностного материала, предназначенного для превращения в медь, железную руду, а также в нефть.
Первые коммерческие развертывания системы Komatsu AHS происходили еще в 2008 году на медном руднике Кодрико Габриэла Мистраль (Gaby) в Чили, а также на железнорудном руднике Рио-Тинто в Австралии. С тех пор рост производства шел по экспоненте. В 2016 году была пройдена отметка в 1 млрд тонн, в конце 2017 года — 1.5 млрд тонн. Этот результат обеспечили более, чем 130 автономных грузовиков, находящихся в эксплуатации на сегодняшний день.
Система Front Runner AHS работает круглосуточно, перевозя медную и железную руду, а также нефтеносные пески на семи участках на трех континентах. В ближайшие 7 лет на канадских нефтеносных песках развернут еще 175 автономных самосвалов. Соответствующий контракт был подписан Komatsu с компанией Suncor Energy, работающей на нефтеносных песках Альберты, Канада.
К 2019 году систему FrontRunner на испытательном полигоне в Тусоне, Аризона, перевели на использование частной сети 4G/LTE. Соответствующее решение Future X предоставила компания Nokia. Подключение роботизированных грузовиков к стандартизованным 3GPP сетям связи 4G/5G может вскоре стать трендом.
2019.01 Автономную систему перевозок FrontRunner компании Komatsu America Corp. перевели на работу с частной сетью 4G/LTE. Компания Komatsu завершила годичные испытания системы автономных перевозок на испытательном полигоне в Тусоне, Аризона, США. В рамках общей программы испытаний также проверялось подключение элементов системы перевозок к частной сети LTE, предназначенной для горнодобывающей компании. Соответствующее решение Future X представила компания Nokia.
2017.02 BHP Billiton, крупнейшая в мире добывающая компания, также осваивает беспилотные грузовики на железных шахтах в Австралии.
2017.02 Роботизированные самосвалы используются для автономной перевозки железной руды на четырех шахтах Западной Австралии компанией Rio Tinto (69 штук в 2015 году, 73 — на конец 2016 года). Грузовики получают сырье с роботизированных буровых установок и отвозят их к поездам, которые также планируется сделать беспилотными.
2017.02 Лидирующий канадский нефтедобытчик Suncor Energy испытывает аналогичное оборудование на песчаных полях Альберты. Испытания самосвалов-роботов начались в Канаде еще в 2013 году, в 2015 году был подписан контракт на закупку 175 роботизированных самосвалов Komatsu для Suncor Energy.
2008 Компания Komatsu впервые внедрила систему автономных перевозок в коммерческом режиме еще в 2008 году на медном руднике Кодрико Габриэла Мистраль (Gaby) в Чили.
Volvo, Швеция
источник фото: motor.ru
Это часть проекта Electric Site полностью автономного процесса разработки карьера. Предполагается, что все этапы работы будут происходить автономно — добыча, первичное дробление и перевозка.
Другой проект с участием автономных самосвалов Volvo — это транспортировка известняка из карьера норвежской горнодобывающей компании Brønnøy Kalk AS в близлежащий порт. На 5 километровом участке, включающем туннели, задействовано шесть автономных грузовиков Volvo FH.
В течение 2018 года шла тестовая эксплуатация этого проекта, до конца 2019 года он, как ожидается, перейдет в режим коммерческой эксплуатации. Интересна модель взаимодействия горнодобытчиков и Volvo — RaaS. Компания не закупала роботизированные грузовики, оплачивая Volvo за каждую перевезенную тонну груза. При погрузкой Volvo FH ими управляет оператор фронтального погрузчика.
2018.08.31 Компания Volvo Construction Equipment начала испытывать прототипы автономных электрических самосвалов-тележек HX2 на территории карьера Викан-Кросс в окрестностях Гетеборга, Швеция. Это часть проекта Electric Site полностью автономного процесса разработки карьера. Предполагается, что все этапы работы будут происходить автономно — добыча, первичное дробление и перевозка. / quto.ru
БЕЛАЗ-75131, БЕЛАЗ, Беларусь
Также разработано роботизированное управление, которое может устанавливаться на любую модель карьерного самосвала БЕЛАЗ с электромеханической трансмиссией грузоподъемностью от 90 до 450 тонн.
По состоянию на 2018 год самоуправляемый БЕЛАЗ есть, например, в распоряжении российского ПАО “ФосАгро”. Один оператор может дистанционно управлять сразу несколькими машинами, задавая им места разгрузки. У грузовика есть три режима работы — обычный с водителем, дистанционно управляемый, автоматизированный. Скорость движения — 15 км/ч.
БЕЛАЗ начал заниматься серийным производством модели 7513R.
Стратегическим партнером «БЕЛАЗ» в разработке беспилотных автомобилей является «ВИСТ Групп» — проект называется «Интеллектуальный карьер». В 2010 году в рамках этого проекта был представлен телеуправляемый карьерный самосвал БЕЛАЗ-75131 грузоподъемностью 130 тонн с электроприводом постоянного тока. В 2015 году была показана роботизированная версия этого автомобиля. Также разработано роботизированное управление, которое может устанавливаться на любую модель карьерного самосвала БЕЛАЗ с электромеханической трансмиссией грузоподъемностью от 90 до 450 тонн. / abw.by
2 карьерных 7513R на март 2019 года уже поставлены в Россию для работы на Абаканском разрезе в Хакасии. В планах — до конца 2019 года отправить в Россию еще 5 беспилотных самосвала. Сборка первых двух уже завершена, идет наладка систем узлов.
В 2018 году самоуправляемый БелАЗ есть, например, в распоряжении ПАО «ФосАгро». Один оператор может дистанционно управлять несколькими машинами, направляя их к местам разгрузки. / retail-loyality.org
В марте 2019 года компания БЕЛАЗ показала БЕЛАЗ-7513R — с интеллектуальной системой управления нового поколения. Система Vist Robotics обеспечивает более развернутое сканирование окружения, в том числе, несмотря на сложные погодные условия. Челночный режим движения обеспечивает меньший износ покрышек, а также сокращает на 12% время движения по маршруту. В дальнейшем планируется автоматизировать также погрзочные работы, машина-погрузчик сможет соотносить перемещения с положением самосвала. Уже работающие на объектах самосвалы планируется обновить автоматизированными системами в ближайшее время. / sb.by
Название неизвестно, Inner Mongolia North Heavy Industries Group Co., Ltd, Китай
Автономный карьерный самосвал представлен в феврале 2019 года. Погрузка и разгрузка осуществляются также автономно, самосвал рассчитан на круглосуточную работу. Длина новинки составляет 12.7 метров, высота — 5.2 метра, грузоподъемность — 110 метрических тонн. В составе оснащения: модуль GPS, лазерные сенсоры расстояний и 5G. Первые грузовики приступят к работе в 1h3019. По словам разработчиков, 7 “беспилотников” демонстрируют ту же эффективность, что и 9 управляемых людьми самосвалов. Топливные издержки сокращаются на 6%, а выработка повышается на 49%.
2019.02.06 Китай автоматизирует добывающий комплекс?
Выводы и прогнозы
Напрашивается вполне очевидный прогноз. Рост себестоимости горнодобычи, в том числе, за счет роста заработной платы, уменьшает сроки окупаемости автоматизации процессов добычи и транспортирвки. Это стимулирует горнодобывающие компании все активнее внедрять самоуправляемую технику. Дополнительные стимулы — это снижение числа несчастных случаев и повышение эффективности использования техники за счет отказа от использования человеческого труда в процессе добычи и транспортировки.
Большим интересом будут пользоваться комплексные решения — централизованные системы, позволяющие работать с флотом автономного транспорта и другими системами.
robotrends.ru
Самые большие грузовики (карьерные самосвалы) в мире. / Выхлопная труба / magSpace.ru
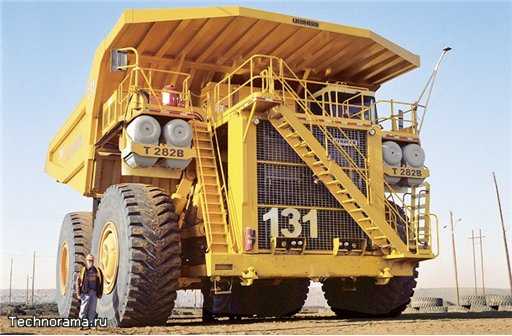
Liebherr T 282 B
Им не место в городе. Им не место на трассе. Им вообще нет места на дорогах. Потому, что еще пока не создали таких дорог, по которым спокойно смогли бы перемещаться карьерные самосвалы. Тысячи лошадиных сил мощности, десятки тысяч ньютон-метров крутящего момента, сотни тонн собственной массы – постоянная среда обитания всего этого великолепия рудники и открытые разработки полезных ископаемых.
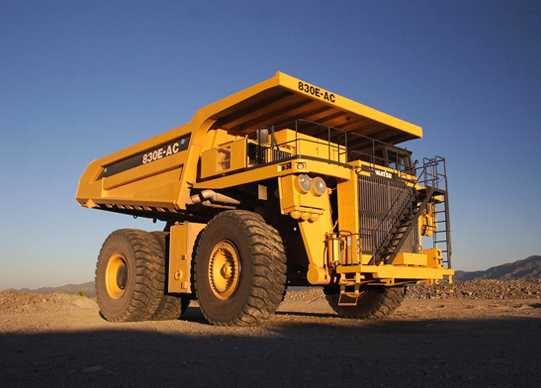
Шанс увидеть живьем карьерный самосвал выпадает немногим, ведь среда их обитания – карьеры, рудники и открытые разработки.
И, несмотря на то, что сектор применения автомонстров очень специфичен и ограничен, а стоимость каждого самосвала составляет несколько миллионов долларов, конкуренция очень высока. Но в отличие от обычных автомобилей, где борьба идет за комфорт, динамические характеристики и дизайн, здесь самые-самые определяются по другим параметрам, самый главный из которых – грузоподъемность. Так, отдельные представители тяжелой техники за один раз способны перевезти в своем кузове более 350 тонн породы! И даже более того, они это делают каждый день, не прерываясь на выходные и праздники. А отдыхает автомобиль только в случае поломки, планового технического обслуживания или по дороге на новое место работы.
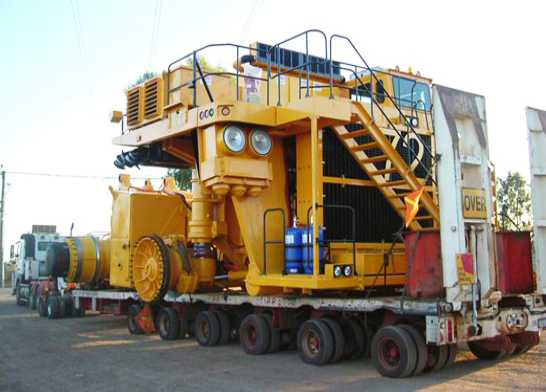
На место работы гиганты отправляются в разобранном виде – асфальтовых дорог, которые без последствий смогли бы выдержать их вес, пока еще не придумали.
Жестоко? Да жестоко, но иначе нельзя. После покупки автомобиль должен сразу отрабатывать немалые затраты на его покупку, и каждая минута простоя обходится владельцу очень дорого. Вот и трудятся огромные исполины практически круглые сутки, ползая по тропам рудников и разработок.
Если посмотреть на эту картину из окна вертолета или со смотровой площадки, то все кажется достаточно органичным: узкие тропы и обычные грузовики. Масштабы происходящего начинаешь осознавать, только если окажешься в непосредственной близости. И тогда маленькие тропы превращаются в широченные плато, на которых спокойно разъезжаются исполины высотой с хороший двухэтажный дом, и шириной почти в десять метров, везущие в кузовах по небольшому Эвересту. И с высоты человеческого роста, которая, кстати, вполовину меньше высоты колеса карьерного самосвала, думать о том, что «вот та громадина чуть поменьше вот той» не приходится.
И все-таки они различаются. Так, например, японский Komatsu 930E-3SE в импровизированной четверке самых больших автомонстров можно поставить на четвертое место.
4 место. Komatsu 930E-3SE.
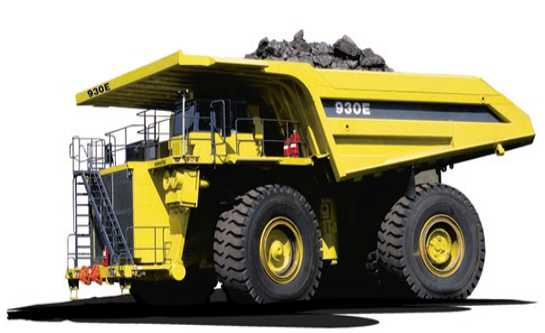
Komatsu 930E-3SE — флагман японского производителя тяжелой техники, полная масса автомобиля – 504 тонны, а мощность двигателя – 3500 лошадиных сил.
Автомобиль длиною чуть менее 15,5 метров, способен перевозить в своем «чреве» до 290 тонн груза. А его полная масса составляет ни много, ни мало 500 тонн! Для того, чтобы сдвинуть такую громадину с места под капотом (в переносном смысле этого слова) расположен 18-ти цилиндровый турбодизельный двигатель мощностью 3500 лошадиных сил, которые он развивает при 1900 оборотах в минуту.
Кстати, этот силовой агрегат может похвастаться не только высокой мощностью и убийственным крутящим моментом, но и немалым весом – 10 тонн! И эта цифра не кажется совсем фантастической, особенно, после того как узнаешь, что в его системе смазки с мокрым картером «плещется» 340 литров моторного масла, а в системе охлаждения все 719 литров антифриза.
В отличие от обычных автомобилей, где маховик двигателя соединен с ведущими колесами через коробку передач, в карьерных самосвалах самой популярной является другая схема тягового агрегата. Двигатель всю свою мощность отдает не механической трансмиссии, а генератору переменного тока, который в свою очередь питает тяговые электромоторы.
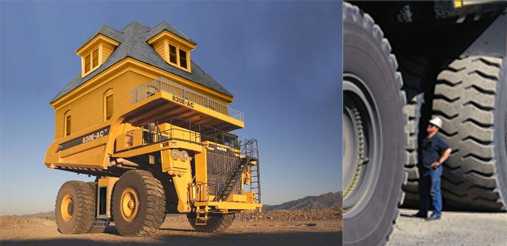
Размеры грузовика действительно огромны – в своем кузове он может перевезти загородный дом средних размеров.
Кстати, электродвигатели, составляют часть задней оси, а значит, являются рабочими образцами пресловутых мотор-колес, которых мы никак не дождемся в легковом секторе. Крутящий момент от электродвигателей передается на гигантские колеса с посадочным диаметром покрышки 63 дюйма не напрямую, а через компактные редукторы (так объем масла, необходимый для работы каждого редуктора составляет всего 95(!) литров «трансмиссионки»). С таким силовым агрегатом, максимальная скорость Komatsu 930E-3SE составляет 64,5 километров в час, что для такой махины совсем не мало, и проблема тут состоит не в том, чтобы ее разогнать, а в том, как остановить.
Над этой задачей трудится гибридная тормозная система, состоящая из трех подсистем: основной, вспомогательной и стояночной. Основная система – гидравлическая, многодисковая, с раздельными контурами передней и задней оси и масляным охлаждением тормозных дисков. Максимальное давление тормозной жидкости в контуре составляет 172 атмосферы и при этом во время торможения общая площадь поверхности трения составляет почти 10 квадратных метров!
Но даже такая система не может в одиночку справляться с гигантом, поэтому ей в помощь трудится вспомогательная – электродинамическая система торможения. Во время торможения тяговые электромоторы переключаются в режим генераторов, и вся вырабатываемая ими электроэнергия превращается в тепло на нагрузочных резисторах. Мощность, рассеиваемая на резисторах, в пике может быть более 4000 киловатт! В то время как среднее значение этого параметра составляет 2900 киловатт.
Стояночная тормозная система – с сухими тормозными дисками, способна удерживать полностью загруженный автомобиль на 15% уклоне. Привод цилиндров – механический пружинный, управление – гидравлическое.
3 место. БелАЗ 75600.
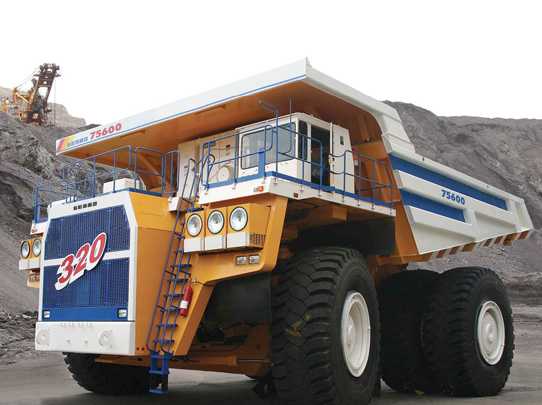
Почти что отечественный БелАЗ 75600 за час работы потребляет большее 500 литров дизельного топлива.
Еще больше руды, чем Komatsu 930E-3SE, способен перевезти БелАЗ 75600 – грузовик, который с запасом входит в элитный класс 300-тонных карьерных самосвалов. Его максимальная грузоподъемность составляет 320 тонн, а полная масса загруженного автомобиля — 560 тонн. При этом его длина даже меньше чем у японского тяжеловеса – всего 14,9 метра.
В качестве силового агрегата на БелАЗе используется 18-ти цилиндровый V-образный турбодизель Cummins QSK78-С объемом 77,6 литров. Номинальная мощность двигателя – 3546 лошадиных сил, крутящий момент – 13771 Нм. Схема силовой установки – комбинированная с генератором переменного тока и двумя тяговыми электродвигателями фирмы Siemens мощность по 1200 киловатт каждый. Максимальная скорость автомобиля – 64 км/час. Кстати, средний расход топлива в час у такой махины колеблется у отметки 500-550 литров солярки в час, так что стандартного 4375-литрового бака хватит как раз на рабочую смену.
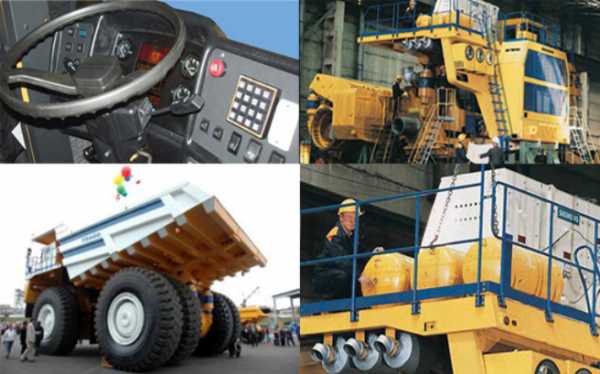
На БелАЗ 75600 используется объединенная гидросистема, которая включает в себя опрокидывающий механизм платформы, тормозную систему и рулевое управление. Все это дело приводит в действие аксиально-поршневой двухсекционный насос переменной производительности. Общий объем гидравлической системы – 600 литров масла, давление в рабочем контуре – 165 атмосфер.
Рулевое управление у БелАЗа с аварийным контуром – в случае отказа основной системы или остановки двигателя, в работу вступают пневмогидроаккумуляторы, запаса энергии которых хватит для того, чтобы совершить пару маневров.
Подвеска – полностью зависимая, спереди установлено по 2 масляных амортизатора с газовым подпором, сзади по одному. Амортизаторы отличаются сверхмалыми рабочими ходами поршней: для передней оси 200 мм, для задней 170 мм.
Кстати, в плане формирования списка дополнительных опций, карьерные самосвалы ничем не отличаются от легковых автомобилей, естественно с поправкой на специфику. Так для БелАЗ 75600 можно дополнительно заказать кондиционер, дополнительный отопитель, систему контроля давления в шинах и даже подогрев зеркал заднего вида! Кроме того, самосвал, можно оснастить и весьма специфическими опциями, чего стоит одна система предупреждения о приближении к высоковольтным линиям или система контроля загрузки автомобиля.
2 место. Caterpillar 797B.
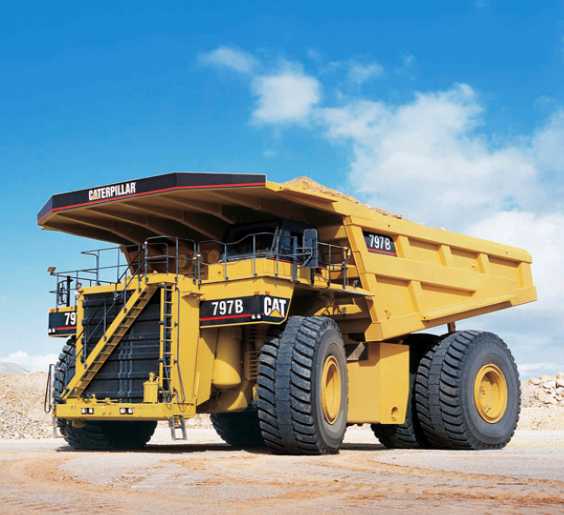
Caterpillar 797B по конструкции – обычный грузовой автомобиль, разве что очень большой.
На втором месте заслуженно обосновался представитель наиболее известного производителя тяжелой техники — Caterpillar 797B. Исполин с полной массой почти 624 тонны, способен взять на борт 345 тонн груза. При этом он обладает достаточно экзотичной для карьерных самосвалов конструкцией. Хотя, если посмотреть с обычной автомобильной точки зрения – Caterpillar 797B построен по традиционным, даже скорее классическим канонам: заднеприводный автомобиль с передними управляемыми колесами, турбодизельным двигателем и гидромеханической трансмиссией.

Силовой агрегат у Caterpillar 797B поражает воображение: 24 цилиндра, 117 литров рабочего объема, 3550 лошадиных сил и 16 000 Нм крутящего момента!
В передней части самосвала расположен огромный 24-х цилиндровый двигатель рабочим объемом цилиндров 117 литров! Для того, чтобы создать такой мотор, инженерам фактически пришлось взять два двенадцатицилиндровых двигателя Cat 3512B и совместить их воедино. Несмотря на большой объем, мощность двигателя всего на 4 лошадиных силы больше, чем у БелАЗа. Такую «скупость» производитель обещает возместить повышенным ресурсом двигателя, и именно с этой целью были ограничены максимальные обороты. Зато крутящий момент здесь действительно рекордный: больше 16 000 Нм!
От двигателя крутящий момент через короткий карданный вал передается в самую большую коробку переключения передач в мире! Гидромеханическая планетарная коробка имеет 7 ступеней и управляется компьютером. Вообще Caterpillar 797B по праву считается одним из самых напичканных электроникой карьерных самосвалов. Центральный блок контролирует сотни параметров и в зависимости от внешних условий, корректирует работу двигателя, трансмиссии и тормозной системы. Так во время старта груженого самосвала или подъема в гору, система кратковременно увеличивает крутящий момент на 22% от номинального значения и выбирает оптимальные моменты для переключения передач, а во время торможения не допускает блокировки колес и увода автомобиля с траектории.
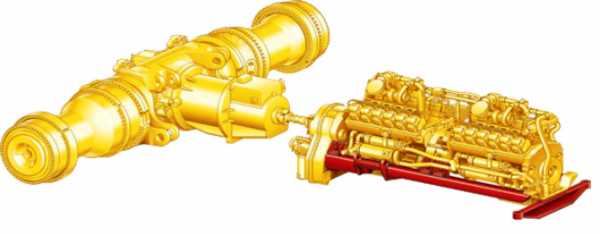
Любовь американцев к «автоматам» и объемным моторам дала о себе знать и в тяжелой технике — Caterpillar 797B может похвастаться самой большой трансмиссией и самым большим двигателем.
Над чем действительно пришлось потрудиться основательно, так это над тормозной системой. Если у конкурентов, основную часть работы на себя берут электродинамические тормоза, то здесь вся нагрузка приходится на гидравлику. Чтобы гарантированно останавливать полностью загруженный автомобиль суммарную рабочую площадь тормозных дисков пришлось увеличить до 33 квадратных метров – это более чем втрое больше, чем у того же Komatsu. Кроме этого тормоза имеют мощную масляную систему охлаждения и резервный контур с гидравлическим замком – как только давление в контуре падает – тормозные цилиндры под действием пружины останавливают автомобиль.
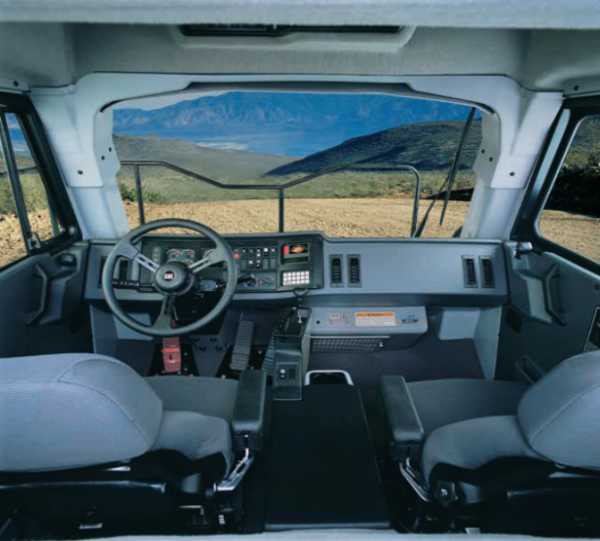
Две педали, руль, селектор «автомата» — рабочее место водителя вполне себе заурядно.
Кстати, Caterpillar 797B может похвастаться несколькими рекордами: самый большой двигатель – 117 литров рабочего объема и 24 цилиндра; самая большая трансмиссия, самая большая максимальная скорость – почти 68 км/ч; самый вместительный топливный бак – 6800 литров. Но все-таки первое место ему занять мешает…
1 место. Liebherr-T282B.
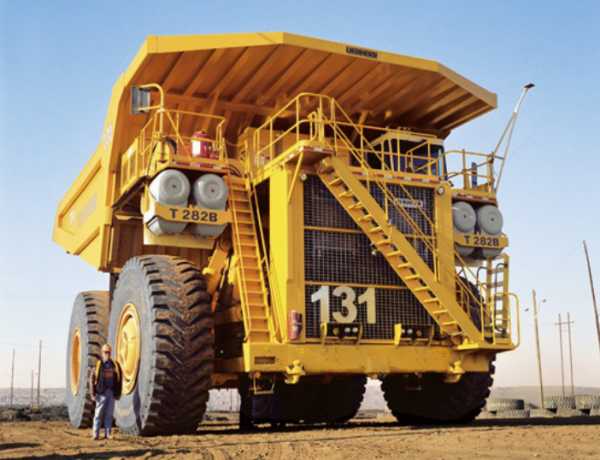
Восьмое чудо света. Именно так прозвали Liebherr-T282B во время премьеры, на строительной выставке в Герамнии.
Абсолютный рекордсмен не только по величине, но и по грузоподъемности. Изобретен в Германии компанией Liebherr в 2004 году. Предназначен для работы в карьерах и перевозки ископаемых, строительных материалов, а также иных грузов. Параметры его размеров поражают своими масштабами:
Высота -7.4 метра
Ширина – 9 метров
Длинна – 14.5 метров
Вес – 592 тонны.
Грузоподъёмность — 363 тонны.
Больше груза, чем Liebherr-T282B пока не может взять на борт ни один грузовик в мире. При этом его снаряженная масса на 50 тонн меньше чем у Caterpillar 797B – 230 тонн против 280 у американца. Именно по способности перевезти как можно больше груза при наименьшей собственной массе оценивается совершенство конструкции, и по этому параметру Liebherr-T282B превосходит всех своих конкурентов.
Впервые был представлен на Мюнхенской строительной выставке, куда его доставили в разобранном состоянии на 5-ти огромных грузовиках. Как только самосвал представили публике, пресса сразу провозгласила его «восьмым чудом света».
Свои уникальные способности немецкий богатырь приобрел благодаря новому конструкторскому решению: на каждой оси у автомобиля производители поместили по три гигантских колеса высотой в 3,5 метра (это два человеческих роста!). А в каждом из колес установили еще и электромотор, который питается от мощнейшего 20-ти цилиндрового дизельного двигателя. Кстати, новый двигатель DDC/MTU (Detroit Diesel), мощностью 3650 лошадиных сил (2725 к.в), тоже оказался самым мощным в мировой автопромышленности. Сегодня такое чудо техники стоит 2.5 миллиона евро. Единственное, что впечатляет меньше всего, так это скорость T282B. При всех своих достоинствах, громадина передвигается неспешно и размеренно – 64 км/ч, именно так, как и подобает победителю.
Автомобиль может комплектоваться двумя двигателями: либо 18-ти цилиндровым Cummins QSK 78 (как на БелАЗ 75600) массой 11300 килограмм, либо более легкой и мощной «двадцаткой» Detroit Diesel, объемом 90 литров, мощностью 3650 л/с. Схема силовой установки классическая для карьерных самосвалов – двигатель приводит в действие генератор переменного тока, а тяговой силой являются электромоторы Siemens.
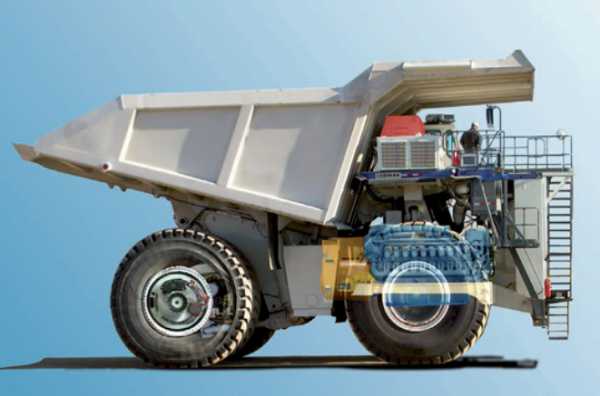
20-ти цилиндровый двигатель с генератором переменного тока расположен над передними колесами, тяговые электродвигатели – вместо задней оси.
Тормоза – гибридные. Основную работу на себя берет электродинамическая тормозная система, превращая тяговые электромоторы в генераторы, которые в свою очередь гасят выработанную энергию на специальных резисторах. В помощь им трудятся гидравлические дисковые тормоза: по одному тормозному диску на передних колесах и по паре на задних.
В отличие от других самосвалов, где одна гидравлическая система обслуживает, рулевое управление, тормоза и систему опрокидывания кузова, здесь две первых системы снабжены собственным независимым контуром объемом 1060 литров с резервным гидравлическим аккумулятором.
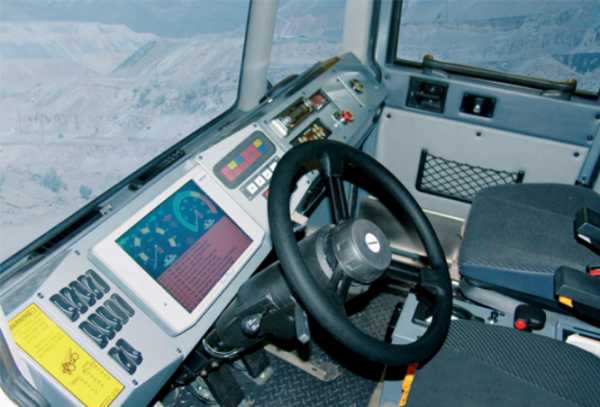
На жидкокристаллическую приборную панель, помимо технических данных может выводиться изображение с видеокамер, расположенных по периметру кузова.
Управлять такой махиной совсем непросто, и ошибка водителя может стоить действительно дорого, поэтому в автомобиле сделано все для того, чтобы облегчить водителю рабочую смену. В кабине хорошо защищенной от внешнего шума и пыли, педали и руль находятся на своих привычных местах, а перед глазами водителя – прогрессивная жидкокристаллическая панель приборов. От жары водителя спасает кондиционер с мощной системы фильтрации воздуха, от холода – не менее мощная печка, ну а от скуки – современная аудиосистема, и осознание того, что твоим рукам подчиняется самый большой автомобиль в мире.
В 70-е годы пытались использовать трёхосные самосвалы, как например Terex Titan и WABCO 3200B, но такие схемы в карьерах не прижились.
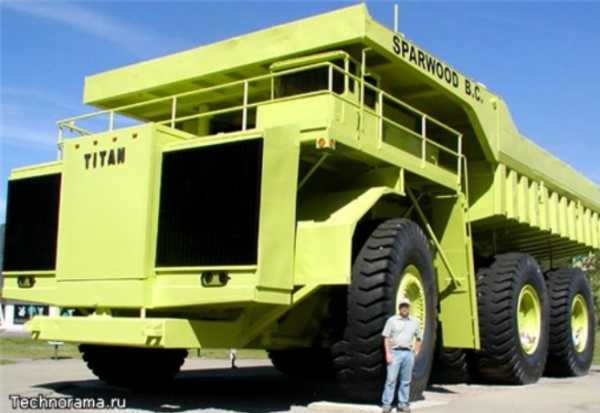
Titan Terex 33-19
На снимке показан гигантский карьерный самосвал «Терекс Титан» (Terex Titan), модель 33-19, детище канадского филиала концерна «Дженерал Моторс». Автомобиль был произведен в единственном экземпляре в 1974 году. При массе «нетто» в 260 тонн, «Титан» имел грузоподъемность в 350 тонн; таким образом полный вес составлял аж 610 тонн! Внешние габариты были таковы: 20,09 х 7,57 х 6,88 м; а при поднятом кузове высота достигала 17 метров. Махину приводил в действие двухтактный шестнадцатицилиндровый дизель от тепловоза мощностью в 3300 л.с. (2,460 кВт), спаренным с генератором. Генератор подает силу на четыре электрических тяговых мотора, расположенных на каждом из задних колес.
«Терекс Титан» и поныне является самым длинным карьерным грузовым автомобилем из когда-либо построенных, хотя по такому параметру, как грузоподъемность, он оказался уже превзойденным. Имеется в виду такие карьерные самосвалы, как «Терекс»/«Юнит Риг» МТ5500, «Катерпиллер-797», «Юклид R280»/«Хитачи EH 4500», «Комацу 930Е» и «Либхерр Т282». Все эти двухосные машины имеют полезную нагрузку в 330-390 тонн.
Построенный в далеком 1974 году в GM’s London, Ontario Plant, он тестировался 12 месяцев в Калифорнии. В 1978 году он был полностью смонтирован в компании Sparwood BC для Kaiser Resources Ltd. Он перестал использоваться на угольных шахтах в 1990 году, после 12-летней не особо выгодной эксплуатации уникум чуть было не пошел на слом; но, благодаря энтузиастам из канадского Спарвуда (Британская Колумбия), был спасен и ныне экспонируется в этом городе на радость детишкам и туристам.
И ещё новость по теме:
Американское подразделение компании «Komatsu» будет выпускать карьерные самосвалы с электроприводом «930E-4», оборудованные автономной системой тяги «FrontRunner», которая позволит машинам работать без водителей. Самосвалы с системой «FrontRunner» смогут перевозить 390 тонн вскрышной породы и руды без помощи водителей. Такой вид автономной работы значительно повысит производительность в горнодобывающей промышленности, особенно на шахтах, где бывает очень трудно обеспечить достаточное количество рабочей силы из-за дальности местонахождения.
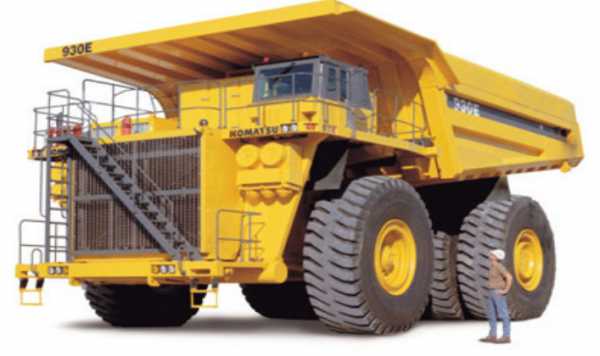
Komatsu 930E-4
Карьерный самосвал оснащен двигателем мощностью 2700 л.с. и усовершенствованным электроприводом переменного тока, что позволяет машине, полный вес которой составляет 500 тонн, двигаться со скоростью 60 км/ч.
источник: TechnoramA
magspace.ru
Карьерные самосвалы: борьба концепций Сравнение эксплуатационных качеств карьерных и шоссейных самосвалов
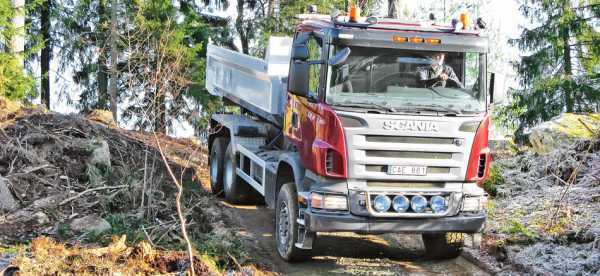
Специализированный карьерный автотранспорт широко применяется как на открытых горных работах, так и при строительстве крупных объектов, ирригационных сооружений. Удельный вес карьерного автотранспорта в технологических перевозках на предприятиях горнодобывающей промышленности сегодня составляет около 70%. И доля автоперевозок только растет.
Возьмем для сравнения эксплуатационных качеств карьерного автотранспорта грузоподъемностью (далее – г/п) от 30 до 60 т с набирающими популярность в этой же рыночной нише шоссейными самосвалами в качестве примера, пожалуй, самую востребованную на территории СНГ технику БЕЛАЗ.
«БЕЛАЗ-ХОЛДИНГ» является крупнейшим мировым производителем карьерных самосвалов г/п от 30 до 450 т. Сегодня техника с маркой «БЕЛАЗ» успешно эксплуатируется в хозяйствах горнодобывающих комбинатов на территориях различных стран мира.
Самосвалы г/п от 30 до 60 т широко и успешно используются в небольших строительных и угольных карьерах с подготовленными технологическими дорогами, а также при строительстве крупных ирригационных сооружений. Однако в последние годы в данном диапазоне грузоподъемности в местах эксплуатации наблюдается массовое внедрение специализированных автосамосвалов на базе шоссейных грузовых автомобилей (Scania, Reno, Volvo, Tatra, Howo и др).
Данный вид машин отличается увеличенной мощностью двигателя, увеличенным объемом кузова, усилением рамы и элементов подвески по сравнению с классическими шоссейными самосвалами. Однако общая компоновочная схема не имеет принципиальных отличий от шоссейного варианта – количество мостов от трех и более, лимитированные габариты по ширине, устройство рамы, трансмиссии и подвески. Надо отдать должное производителям данного вида автотранспорта, так как г/п шоссейных самосвалов сравнялась уже с г/п классических карьерных, то есть от 30 т и выше. При этом цена на новый автомобиль ощутимо ниже, чем на карьерный той же грузоподъемности. Стараясь снизить капитальные затраты, владельцы предприятий все чаще присматриваются к данным машинам, приобретают их для замещения и обновления парка карьерных самосвалов. И как утверждают представители компаний-производителей, после перехода на новый вид транспорта экономические показатели автоперевозок не только не возрастают, но даже и снижаются. Однако скоротечные оценки не всегда объективны, и перед принятием решения о замене одного вида машины на другой надо постараться качественно рассмотреть и сравнить все показатели.
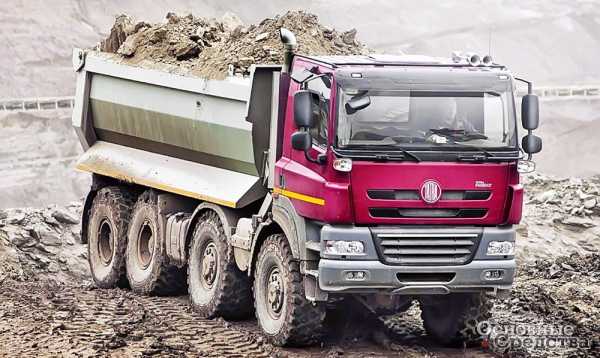
Центр тяжести и рама
Карьерный автотранспорт эксплуатируется в самых разноЖЖЖобразных климатических, горно-геологических и дорожных условиях. Большинство горных предприятий в России расположены в зонах резко континентального климата. Низкая (до –40 °С и ниже) температура зимой с сильным ветром, высокая температура летом (до +40 °С). В горной местности самосвалы работают при пониженном атмосферном давлении, что снижает мощность двигателей и увеличивает расход топлива. Классический рамный автосамосвал создавался именно под условия сложной дорожной обстановки горного предприятия. И речь тут идет в первую очередь не о проходимости вязких заболоченных или запесоченных участков – речь в большей степени о профиле дороги. Для карьерного автотранспорта характерны небольшие расстояния перевозки (от 1 до 5 км), движение по дорогам со сложно-переменным профилем и большим числом крутых поворотов, по временным дорогам с плохим покрытием.
Продольный профиль карьерных дорог представляет собой чередование подъемов и спусков разной величины и длины. Продольные уклоны дорог достигают 10–12%, а на отдельных коротких участках и более того (как в поперечном, так и продольном направлении). Двигаясь по такой дороге, самосвал испытывает воздействие знакопеременных опрокидывающих моментов, поэтому для него важен показатель отношения высоты центра тяжести груженого автомобиля к его ширине. Колея у карьерных самосвалов ощутимо шире, чем у шоссейных, а центр тяжести груза внутри грузовой платформы значительно ниже, чем в кузове шоссейного самосвала. Следствием этого является бóльшая устойчивость «карьерника» при опрокидывании и соответственно бóльшая скорость транспортировки, меньшие требования к состоянию поперечного профиля дороги.
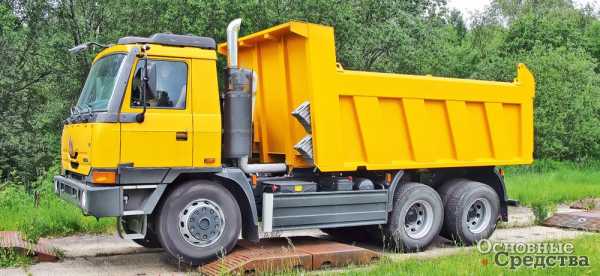
Становой хребет самосвала – его рама. Рама карьерного самосвала разительно отличается от рамы обычного грузового автомобиля. Она выполнена таким образом, чтобы выдерживать высокие ударные и скручивающие нагрузки. Профиль карьерных дорог требует применения колес большого диаметра и ширины, что увеличивает дорожный просвет и влияет на тяговые характеристики. В то же самое время увеличение высоты машины уменьшает ее устойчивость, поэтому профиль рамы сконструирован так, чтобы максимально снизить центр тяжести груженого автомобиля.
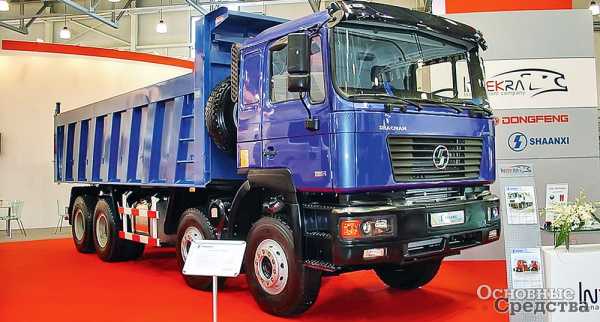
Соотношение размеров и параметров
Традиционно карьерные самосвалы создаются для работы в комплексе с карьерными экскаваторами. Следует отметить, что в процессе проектирования стараются увязать самые различные параметры. Конечно, важным является правильное соотношение размеров ковша и кузова транспортного средства. Ширина кузова должна позволять производить эффективную разгрузку ковша без просыпей, регулировать укладку горной массы. Имеет значение количество разгружаемых ковшей. Подсчитано, что наибольшая эффективность работы экскаваторно-автотранспортного комплекса достигается при условии, когда количество разгружаемых ковшей в кузов транспортного средства составляет три – пять.
Соответственно связаны размеры рабочей площадки с рабочими параметрами экскаватора и радиусами поворота самосвала. В стесненных условиях рабочей площадки карьерный самосвал должен становиться под загрузку и покидать ее при минимуме маневров. При этом установку самосвала следует производить с таким расчетом, чтобы экскаватор работал с наименьшим углом поворота, обеспечивая при этом наивысшую производительность. Недаром ведущие мировые производители карьерной техники (Caterpillar, Komatsu, Hitachi, Liebherr) предлагают сегодня потребителю комплексное решение, а именно связку экскаватор – самосвалы собственного производства, утверждая, что максимально увязывают параметры техники между собой. Или, как это делают БЕЛАЗ и «ИЗ Картэкс», объединяются для проектирования совместного экскаваторно-автотранспортного комплекса. Если сравнить наименьший радиус поворота у карьерного самосвала и у шоссейного той же грузоподъемности, то у последнего радиус поворота будет больше на 1 м и более. А это потребует расширения площадки, усложнения отработки забоя, лишних перемещений экскаватора. Это прямые потери рабочего времени, усложнение процесса отработки на конкретном участке.
Конечно, ощутить преимущества работы хорошо подобранного комплекса можно только при условии высокой интенсивности горных работ. А это не всегда достигается ввиду экономических реалий, компетентности топ-менеджмента и проч.
Подвеска и шины
При разгрузке ковша экскаватора типа ЭКГ (самый массовый на горных работах в СНГ) горная масса падает единовременно в кузов с большой высоты (от 2,5 м и более). Выдержать такие удары может только специально спроектированная подвеска. Подвеска карьерного самосвала состоит из нескольких пневмогидравлических цилиндров и направляющего устройства, представляющего собой систему продольных и поперечных штанг. Пневмогидравлический цилиндр подвески – пневматическая рессора поршневого типа в комбинации с гидравлическим амортизатором. Такая конструкция позволяет эффективно гасить колебания машины, сглаживать ударные нагрузки. Никакие другие «усиленные рессорные подвески» не способны обеспечить удовлетворительную работу самосвала при эксплуатации внутри карьеров. Рабочие характеристики пневмогидравлического цилиндра отличаются большей энергоемкостью сжатия и отбоя при увеличенном ходе, нежели просто набор рессор. Именно они гасят ударные нагрузки от падения кусков горной массы в кузов самосвала. Подвеска держит машину при движении на «ухабах» временных дорог.
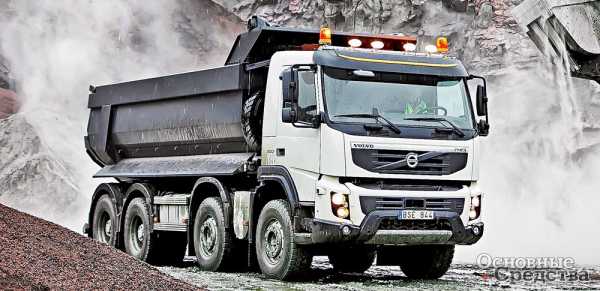
Шины самого легкого карьерного самосвала (г/п 30 т) имеют наружный диаметр 1615±25 мм, ширину профиля 498±15 мм. Более массивные колеса позволяют компенсировать неровности временных дорог, обеспечивают увеличенный дорожный просвет, лучшие условия сцепления. Ходимость шин напрямую зависит от состояния дорожного полотна. Острые куски скальной породы способны вспарывать боковые поверхности колес размером 9.00-22.5, в то время как большое колесо того же БЕЛАЗа просто не почувствует воздействия. Карьерный самосвал режет колею намного меньше, чем шоссейный многомостовый на своих относительно узких колесах (пример – 9.00-22.5). Естественно, для поддержания дорог потребуется меньше затрат, когда по ним ходят только карьерные самосвалы. На практике значения пробега самосвалов БЕЛАЗ г/п 30–60 т до списания составляют (усредненно): для самосвалов г/п 30–45 т – до 450 тыс. км и выше, для г/п 55–60 т – 600 тыс. км и выше. При этом годовой пробег на большинстве карьеров составляет в пределах 60 000–100 000 км в зависимости от среднего расстояния перевозки. Такой объем работы в условиях горных предприятий выполнить автосамо-свалу шоссейного типа практически невозможно.
Также одним из главных недостатков шоссейных самосвалов является отсутствие систем безопасности ROPS и FOPS, без которых работа транспорта внутри карьера запрещена.
У «шоссейников» тоже есть преимущества
Если правильно учесть все аспекты автоперевозок, провести экономический анализ, то применение классических «карьерников» покажет бóльшую эффективность по сравнению с применением шоссейных автосамосвалов.
Однако сфера применения «усиленных, адаптированных» шоссейных самосвалов расширяется. И это факт, который объясняется наличием у них немалых преимуществ. Первое важное преимущество – возможность выезжать на дороги общего пользования, куда закрыт путь карьерному самосвалу. Зачастую существует необходимость транспортировать материал за пределы карьера, а для этого нужно либо возводить технологическую дорогу, либо пользоваться существующей общего назначения.
Второе – больший сцепной вес за счет большего количества приводных мостов и наличия блокировок дифференциалов. Да, по вязким, скользким материалам эти машины идут лучше. Их любят использовать при вывозе вскрышных пород, в которых немалое содержание глины.
Все спекуляции на тему меньшего расхода горючего у шоссейных самосвалов можно отнести на счет плохого контроля расхода топлива на предприятии-перевозчике. КПД дизеля и трансмиссии у обоих типов самосвалов имеют значения одного уровня.
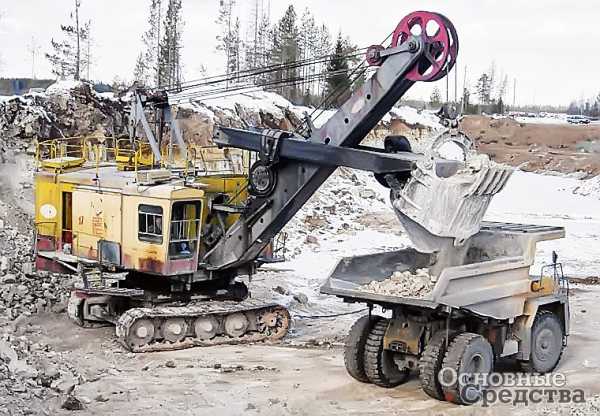
Карьерный самосвал – это мощная маневренная машина большой грузоподъемности, не требующая обустройства шоссейных трасс. Он предназначен для перевозки сыпучих грузов и горных пород по дорогам с прочным основанием, для работы в комплексе с тяжелыми карьерными экскаваторами. Самосвалы БЕЛАЗ создавались с учетом всех этих требований и являют собой классическую отшлифованную конструкцию большегрузных рамных самосвалов с колесной формулой 4х2. В то же самое время существует целый сектор технологических автоперевозок, где автосамосвалы шоссейного типа имеют неоспоримое преимущество перед классическими «карьерниками». Выбор типа автотранспорта должен основываться на качественном анализе условий работы предприятия с учетом времени окупаемости конкретного проекта, ресурса самих автосамосвалов.
os1.ru
Большие карьерные самосвалы – модели, грузоподъемность
Крупная добыча полезных ископаемых или же масштабное строительство различных объектов подразумевает использование современного оборудования и тяжелых технических средств, в частности мощных машин. Одним из видов такой техники считаются большие карьерные самосвалы, которые способны выполнять самую тяжелую и трудоемкую работу. Обладая внушительным видом, такие машины-гиганты демонстрируют не только огромные размеры и нестандартную конструкцию, но и максимальную выносливость, грузоподъемность и превосходные технические характеристики, которые необходимы для выполнения определенных задач.
Одним из отличительных преимуществ карьерного самосвала считается его гигантская грузоподъемность, которая находится в пределах от 100 до 400 тонн, поэтому такие машины запрещены для эксплуатации на дорогах общего пользования. Зато в трудных рабочих условиях карьеров, подобные автомобили не просто значительно облегчают технологический процесс, но и выступают основными «тружениками» производства.
Самосвалы-гиганты
Такой тяжелый вид техники, как карьерные самосвалы, так же, как и другая специализированная техника, насчитывает несколько типов, моделей и модификаций, предназначенных для определенных работ. Модификации, имеющие грузоподъемность от 10 до 50 тонн, представляя собой большие машины в основном для строительства, по сравнению с таким гигантом, как БелАЗ разных модификаций, способного принять на борт груз весом до 450 тонн, кажутся совсем небольшими грузовиками.
На территории России БелАЗ модели 75710 признан одной из самых мощных, тяжелых машин с огромными размерами. Но он не единственный в своем роде – среди модификаций есть модели импортного производства известных в мире производителей строительной и специализированной техники. Именно зарубежный гигант – самый большой карьерный самосвал в мире представлен моделью именитого концерна Komatsu 930 E-3 S E. Это не просто машина внушительных размеров, а техника, обладающая такими характеристиками, как:
- Рабочий объем силового агрегата в 4542 л и мощностью в 3014 л. с.;
- Его грузоподъемность составляет 290 тонн, тогда как принять на борт он может груз, весом до 500 тонн;
- Нагрузка на переднюю ось – 110 тонн, тогда как задняя выдерживает 103 тонны.
В числе его профессиональных и рабочих преимуществ высокая надежность и качество сборки, высокая грузоподъемность, выносливость и точность выполнения технического процесса работы, несмотря на огромные габариты.
Модификации карьерных самосвалов других производителей
Производители тяжелой техники для карьеров и масштабного строительства постоянно усовершенствуют выпускаемую продукцию, увеличивая и мощность, и грузоподъемность тяжелой машины. Поэтому нельзя с уверенностью сказать, что модель карьерного самосвала Komatsu единственная в мире техника, обладающая столь внушительными размерами и характеристиками. По мнению других, модель карьерного самосвала Kress, грузоподъемность которого составляет показатель до 330 тонн, также может быть приравнен к самым большим машинам для тяжелых работ.
Или же еще одна модификация – карьерный самосвал известного производителя строительной и специализированной техники Caterpillar, наиболее часто эксплуатируемый в добыче полезных ископаемых. Его мощность составляет около 4000 л. с. и он обладает такими же внушительными размерами и высокой грузоподъемностью – до 400 тонн. Но самый интересный и уникальный в своем роде карьерный самосвал, выпущенный в единственном экземпляре – это модель Titan 33-19, который после 13 лет тяжелого, но продуктивного труда, был списан в лом, но не уничтожен. Сегодня он выставлен под Спарвудом, как историческая достопримечательность 70-х годов.
Получите выгодное предложение от прямых поставщиков:
Вам будет интересно
spectehnika-info.ru
Обзор крупнейших производителей и российского рынка карьерных самосвалов
На сегодняшний день полезные ископаемые из недр нашей земли помогают добывать огромные машины — карьерные самосвалы, поражающие всех своими габаритами и удивительными структурами.
Карьерные самосвалы класса Ultra Truck появились в XX столетие и носили название Euclid. Выпустила их компания Euclid Crane and Hoist Company, которая в начале своей деятельности ремонтировала и продавала различную технику для возведения домов и сельского хозяйства. И лишь в 30 годы, просмотрев рыночные сводки, фирма приняла решение производить тяжелые грузовики.
С помощью инженеров братьям Армингтон удалось создать новую не просто грузовую машину, а грузовик, выполняющие конкретные цели и задачи. Вид машины был несуразен, но такими конструктивными возможностями не обладал, ни один грузовик. Кузов выполнен в виде ковша и имел заднюю разгрузку, кабину водителя защищал навес, колеса были различны по диаметру. За счет этого самосвал обладал высокой проходимостью. Первый грузовик мог поднимать до 8 тонн груза, и был предназначен для работ только в теплые периоды, так как водительская кабина не имела дверей и отопительной печки.
Данная машина и стала последователем большого семейства современных карьерных самосвалов.
Данный самосвал и явился родоначальником современных карьерных грузовиков. Со временем оптимальной конструкцией самосвала была определена схема с двумя осями, обеспечивающими полный или задний привод, а кузов, которого разгружается, опрокидываясь назад.
Данная карьерная техника делится на две группа:
- с жесткой рамой;
- с шарнирно-сочлененной рамой.
Грузовики, входящие в первую группу, могут иметь гидромеханическую или электромеханическую трансмиссию. При этом, как правило, гидромеханику используют на автомобилях, грузоподъемность которых не превышает 100 тонн, но есть и исключения.
Машины из второй группы отличаются тем, что имеют все ведущие колеса и дополнительный мост для снижения давления на грунт и улучшающий проходимость. В тоже время, они имеют ниже показатели грузоподъемности, чем грузовики с жесткой рамой. Основным направлением использования таких самосвалов стало преодоление бездорожья.
На данный момент есть много крупных производителей самосвалов карьерного класса, но мы рассмотрим лишь самых известных:
- Белаз;
- Terex;
- Caterpillar;
- Liebherr;
- Euclid;
- Komatsu.
Белаз
Ведя разговор о тяжелых машинах, в уме всплывает вначале производитель «Белаз». Огромными монстрами из Белоруссии гордился весь Советский союз. Производство карьерных самосвалов в этой компании все время развивается, они выпускают все новые модели, которые превосходят предыдущие по грузоподъемности и размерам. На данный момент производителем выпускается машина «БелАЗ-75306», весящая 156 тонн и умещающая в свой кузов около 220 тонн полезных ископаемых. Этот вид карьерного самосвала обладает электронной трансмиссией и дизелем в 2300 лошадиных сил, это позволяет развить скорость до 45 км в час. Большей скорости этому суперсамосвалу не нужно, ведь необходимо помнить о сложном управлении этой машины и дорогах, состоящих из грунта.
Машиностроительный завод, производящий «БелАЗов», был возведен в 1948 году в Белоруссии. Своего первенца — БелАЗ-540 завод выпустил в 1961 году, самосвал мог перезвонить до 40 тонн грузов, на тот момент это была большая грузоподъемность. Но производитель не остановился на достигнутом и с каждым разом усовершенствовал свои модели — увеличивая грузоподъемность и объемы машин. Так в 1968 году был выпущен грузовик, обладающий грузоподъемностью до 80 тонн, в 1978 — грузоподъемность увеличилась на 20 тонн, в 1982 — еще на 70, в 90-х годах «БелАЗы» были способны перевозить до 280 т горных пород. Первый мощнейший грузовик «БелАЗ-75600», способный перевозить 320 т грузов появился в 2005 году.
Карьерная машина «БелАЗ-75600» оснащена:
- дизелем с электроуправление;
- передачей с МПУ управлением;
- системой централизованной смазки;
- системой комбинирования тушения пожара с автомат управлением,
- системой видеобзора сзади и с боку;
- кабиной для 2 человек и системой безопасности ROPS.
Белорусский «БелАЗ» может развивать скорость до 64 км в час.
Осенью 2013 года производитель «БелАЗ» выпустил новинку БелАЗ-75710. Этот карьерный самосвал способен перевозить 450 тонн груза. В январе 2014 года эта машина установила рекорд Гиннеса, перевезя 503, 5 тонны груза. БелАЗ-75710 способен развивать максимальную скорость до 67 км/ч.
Terex
General Motors в 1974 году выпустила Terex 33-19 Titan — этот самосвал по-прежнему работает и считается одним из самых огромных грузовиков. Высота этого трехосного гиганта достигает семи метров, а вес — 260 тонн, с наполненным кузовом — 650 тонн. Данный карьерный грузовик работает от двухтактного шестнадцатицилиндрового дизельного двигателя мощностью в 3300 л.с.
Компания Terex была создана в 1968 году путем преобразования организаций в промышленности США. На данный момент Terex — одна из крупных корпораций на земле, которая состоит из 40 различных изготовителей техники и трудится в 120 государствах.
Мощнейшие карьерные грузовики от корпорации выпускает производитель Unit Rig, входящий в группу компании Terex. Представителем этой фирмы в России является «Глобал Технолоджи Групп». Модели ТМТ представлены 9-ю самосвалами на дизельном электрическом двигателе, способными перевозить 109-326 тонн грузов. Недавно появились компактные и экологические грузовики на дизельном электрическом двигателе с приводом переменного тока. Их грузоподъемность составляет 109-326 тонн, а мощность двигателя — 895-2090 кВт.
Caterpillar
Не только Terex 33-19 Titan имеет большую грузоподъемность, в этом его превзошел Caterpillar-797. Данный самосвал способен перевозить свыше 400 тонн грузов. Вес самой машины — 260 тонн, а размеры такие гигантские, что в кузове легко поместиться большое строение из камня. Автомобиль оснащен семи кубометровой канистрой для топлива, так как его расход на 1000 м составляет 783 литра. В движение колеса самосвала приводят два двигателя суммарным объемом 3400 л. с. с несколькими турбинами посредством семискоростной коробки передач на механике, несмотря на то, что есть мнение — использование электротрансмиссии позволяет получить плавное движение, настолько нужное для такого рода машин. На карьерных машинах устанавливают коробки не только семиступенчатые, но и пятнадцатиступенчатые и даже больше. Наивысший скоростной режим Caterpillar-797 просчитать сложновато, так как электросистема, встроенная в него, ограничивает развитие скорости до 65 км в час. Для такого огромного монстра данное ограничение считается разумным, ведь его габариты огромны: длина — 14,5 м, ширина — 9 м, высота — больше 7 м.
Liebherr
Карьерные грузовики огромных размеров и возможностей перевозить большие тонны грузов существуют и Европейского производства. Так одним из представителей является Liebherr T282B — немецкий автомобиль, выпущенный специально для Австралийских, Южноафриканских и Канадских горных обогатительных комбинатов. Данный самосвал весит 222 тонны и может перевозить около 336 тон грузов. Liebherr T282B может развить скорость до 64 км в час, благодаря 20-тицилиндровому двигателю мощностью 3650 л.с. Бак для топлива установлен у грузовика объемом 4 730 л. При поднятом кузове объемы этой махины поражают — он становиться размером с дом из 16 этажей.
Кабина самосвала рассчитана на 2 человек и имеет панель с дисплеем, показывающим не только работу двигателя, его неисправности и много другой необходимой информации. Теперь для отключения двигателя и обесточивания машины не нужно преодолевать кучу степеней, конструкторы установили данную кнопку снизу самосвал недалеко от земли.
Euclid
Карьерные грузовики от компании Euclid — одни из самых старых самосвалов, их производство началось в 1933 году. На данный момент Euclid состоит в промышленном холдинге Hitachi из Японии и носит название Euclid-Hitachi. Эта корпорация выпускает различные карьерные грузовики, способные перевозить 36-282 тонны грузов.
Komatsu
Komatsu Dresser Company летом 1995 года выпустила крупнейший карьерный грузовик Komatsu 930Е, способный перевозить 290 тонн груза. Также у этой фирмы существует еще один дом на колесах Komatsu 830Е с грузоподъемностью 231 тонна. Грузовики оснащены дизель-электрическими двигателями и имеют мощность 1 902 и 1 865 кВт.
Карьерные самосвалы на российском рынке
Наша страна, имея огромные запасы природных ископаемых, входит в число наибольших потребителей разнообразной техники, задействованной в горнодобывающей промышленности. Одну из наиболее важных задач выполняют при помощи карьерных самосвалов.
Наиболее часто на территории страны задействованы следующие типы самосвалов:
- строительно-дорожные, имеющие грузоподъемность 10-30 тонн;
- автомобили, имеющие шарнирно-сочлененную раму и грузоподъемность которых составляет 10-50 тонн;
- автомобили повышенной проходимости с грузоподъемностью до 400 тонн.
Большую часть рынка занимают грузовики, грузоподъемность которых не превышает 40 тонн. Использование карьерных автопоездов также широкого применения не получило.
Основным направлением развития карьерных грузоперевозок является увеличение грузоподъемности грузовиков. Данный параметр, в частности для больших месторождений, оправдывает себя, потому что, увеличив среднюю грузоподъемность с 100 до 300 тонн, позволяет сэкономить на транспортных расходах до 25%.
Не стоит упускать из виду и ни менее интересные варианты оптимизации:
- улучшение проходимости грузовиков;
- более широкое внедрение автоматики в средства управления и диагностики;
- повышение компактности автомобилей при тех же показателях грузоподъемности.
Сейчас отечественный рынок таких грузовиков представлен преимущественно моделями таких производителей как БелАЗ, Volvo, Caterpillar, Komatsu, Terex и Euclid-Hitachi.
В последнее время все большую часть рынка занимает техника, произведенная на территории РФ на предприятиях, созданных совместно с ведущими производителями.
Так на заводе, расположенном в Ленинградской области, в 2011 году был налажен выпуск востребованного самосвала Caterpillar 773Е, грузоподъемность которого составляет 54 тонны, а несколько лет спустя с 2014 года было запущено также производство модели 777G грузоподъемностью около 90 тонн.
В конце 2011 года также была начата российская сборка карьерных грузовиков Komatsu в г. Ярославле, где первой выпускаемой моделью стал 91-тонный HD785-7. И уже в следующем году сошедшие с конвейера самосвалы отправились к своему заказчику.
В это же время совместным предприятием «RM-Terex» в Челябинске было запущено производство карьерных грузовиков Terex, в частности первым стал TR100-RM, с наиболее востребованной тоннажностью 91 тонна.
Рынок в целом после значительного подъема в 2010-2012 годах до 2 тысяч грузовиков в год, на данный момент переживает спад и его объем составляет около тысяч единиц ежегодно.
И хотя количество ввезенной техники с каждым годом уменьшалось, лидирующие позиции продолжают занимать БеЛАЗ, Caterpillar, Hitachi.
Доля техники, поставленной из Белоруссии, занимает до 80%, при этом максимально (около 40%) представлены самосвалы БелАЗ в сегменте вместимостью 120-240 тонн.
Специалисты прогнозируют, что падение рынка уменьшается и в дальнейшем ежегодный рост ожидают от 1 до 7%. Наиболее перспективными для развития называются группы по 90-100, 120-150 и 218-240 тонн.
Согласно данным исследователей ожидается увеличение доли производителей Terex, Cat и Komatsu в сегменте большой вместимости. Но это не скажется негативно на производителе БелАЗ, поскольку вытеснение будет довольно медленным и уменьшение доли будет скомпенсировано ростом рынка в целом.
news-mining.ru
Основные средства Лебединского ГОКа (Часть 1)Обзор карьерных самосвалов одной из крупнейших горнодобывающих компаний России
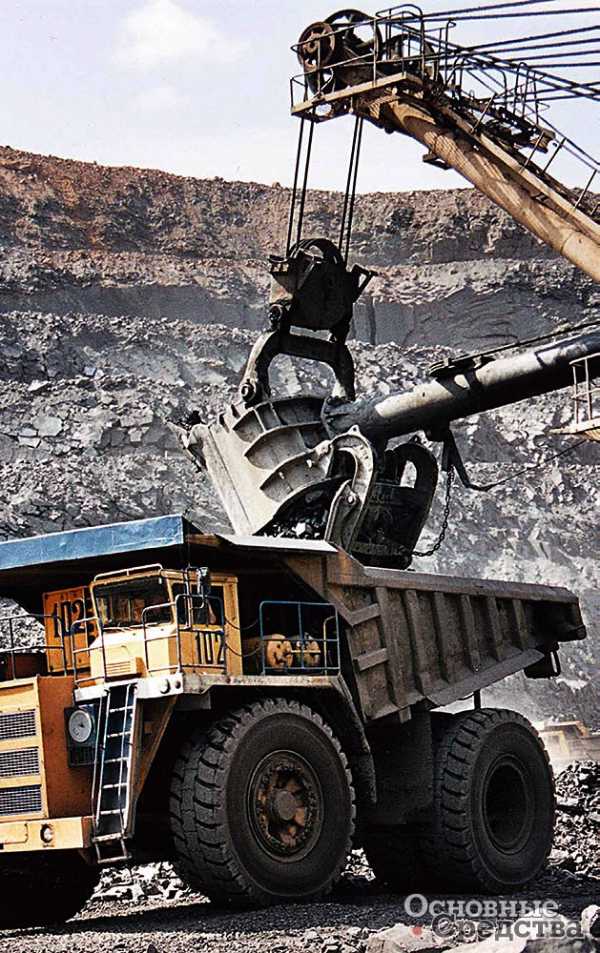
В. Васильев, фото автора
Россию по праву называют мировой кладовой полезных ископаемых. Подтверждением сказанному является, в частности, Лебединский горно-обогатительный комбинат (ГОК) в Белгородской области. Открытый карьер этого гигантского рукотворного сооружения по своим размерам и запасам сырья занесен в Книгу рекордов Гиннесса.
Разработка Лебединского месторождения железных руд Курской магнитной аномалии началась в 1957 г. Сегодня здесь открытым способом добывают железистые кварциты с содержанием железа не более 30%. Лебединский ГОК – одна из крупнейших горнодобывающих компаний России: темпы ежегодной добычи железистых кварцитов превышают 50 млн. т. Десятки отечественных и зарубежных потребителей поддерживают деловые связи с компанией. Размеры открытого карьера достигают 5 км в длину, 3 км в ширину, а глубина находится на отметке около 350 м. Разведанных запасов железной руды при непрерывной добыче хватит на 300 лет!
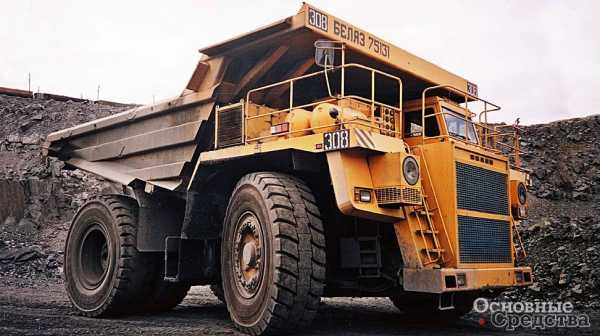
Производственная цепочка на Лебединском ГОКе начинается в карьере. В настоящее время на комбинате применяется циклично-поточная технология разработки месторождения. С помощью буровых станков бурят относительно неглубокие скважины в породе для закладки взрывчатых веществ (обычно жидкой селитры). Их масса определяется возможностью безостановочной работы комбината в течение двух недель. После взрыва и разрушения горного массива экскаваторы, фронтальные погрузчики и бульдозеры обеспечивают погрузку полученной рудосодержащей породы в автомобили-самосвалы, которые транспортируют и разгружают ископаемые на перегрузочных складах, находящихся на более высоких уровнях. Там экскаваторы загружают руду в железнодорожный состав. Применение на верхних ярусах карьера ж.-д. транспорта как промежуточного звена объясняется в несколько раз меньшей стоимостью его эксплуатации по сравнению с автосамосвалами. Конечными пунктами полезного ископаемого являются горнообогатительная фабрика и смежные технологические производства, расположенные в непосредственной близости от карьера.
Чтобы лучше понять, что такое карьер, надо вообразить горную выработку ниже поверхности земли, разделенную на горизонтальные слои, которые проходят и по пустым породам, и по полезному ископаемому. Слои в процессе разработки приобретают вид уступов. Для ведения горных работ предназначены так называемые горизонты, которые представляют собой систему горных выработок, расположенных на одном уровне. Именно на горизонтах располагается основное рабочее оборудование для последующей разработки одного уступа. Расстояние между горизонтами по высоте на Лебединском карьере составляет примерно 15 м.
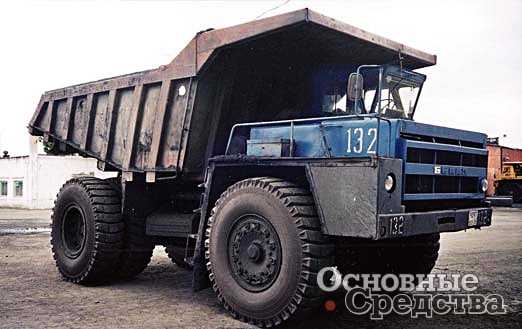
Для транспортировки руды из карьера на промежуточные перегрузочные площадки применяют автомобили-самосвалы. Во второй половине 1960-х годов это были автомобили БелАЗ-540 и -548 грузоподъемностью соответственно 27 и 40 т. Через полтора десятилетия пришла очередь 42-тонных БелАЗ-7548. В 1981 г. в карьере стали работать японские 120-тонные грузовики Komatsu HD1200, к которым в 1986-м прибавилась еще партия таких же машин. В 1988–1990 гг. настал черед отечественных БелАЗ-75191, каждый из которых мог везти 110 т. Последние автомобили Komatsu поступили в 1991–1992 гг. В 1996-м появились американские машины Haulpak 510Е (ныне марка принадлежит Komatsu) грузоподъемностью 120 т.
Сейчас основная транспортная нагрузка ложится на 25 большегрузных карьерных самосвалов, из которых сформирован участок № 1. При этом на долю Komatsu приходится более половины парка. Помимо этого за последние три года приобретены 130-тонные БелАЗ-75131 – по характеристикам технологических дорог Лебединского ГОКа диапазон грузоподъемности (120…130 т) и габаритные размеры самосвалов оказались наиболее подходящими. Чтобы не нарушать технологический цикл транспортировки железорудных концентратов, на работу должно отправляться не менее 17 машин.
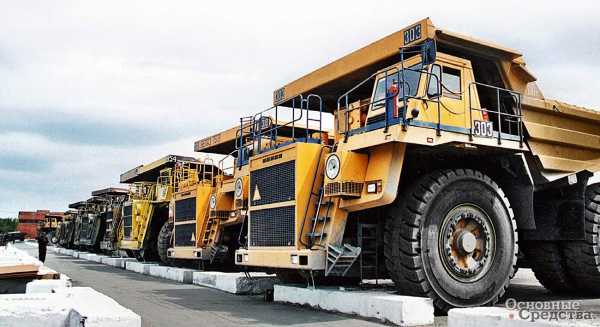
Внешне карьерные самосвалы большой единичной мощности, которые эксплуатируются в карьере, напоминают обычные дорожные самосвалы, но их конструкция имеет существенные отличия. Применение большегрузных самосвалов в сочетании с мощными экскаваторами, фронтальными погрузчиками и бульдозерами позволило резко поднять производительность труда и значительно снизить себестоимость погрузки и транспортировки горной массы. При этом существенно сокращается металлоемкость транспортного оборудования, упрощается строительство карьера, снижаются затраты на прокладку и содержание коммуникаций. Довольно заметно сокращаются сроки строительства карьера и потребность в рабочей силе.
Карьерные самосвалы Лебединского ГОКа – одно из ключевых звеньев комплексного технологического процесса выемки породы и добычи полезных ископаемых, при транспортировке породы в отвалы, а полученных ископаемых – к местам накопления. Большегрузными самосвалами перевозят и грунт на вскрышных работах. Карьерные самосвалы – это внедорожные транспортные средства, поскольку из-за больших нагрузок на ось движение их по дорогам общей сети недопустимо. В карьере машины перемещаются по дорогам относительно небольшой протяженности, выполненным в соответствии со специальными стандартами. Так, например, для самосвала грузоподъемностью 130 т требуются дороги шириной не менее 20 м с толщиной щебеночного покрытия более 1 м. Протяженность внутрикарьерных дорог достигает 40 км. По состоянию опорной поверхности дороги являются постоянными и временными. Расстояние перемещения груза самосвалами в среднем составляет 1,8…2,1 км, а самое длинное плечо откатки достигает 3,6…4 км. Средняя высота подъема грузовиков при транспортировке породы – 70…78 м. Максимальная скорость в карьере не более 30 км/ч; обычно груженый самосвал идет в гору со скоростью 15…20 км/ч. Работу грузовиков в карьере обеспечивают гусеничные и колесные бульдозеры разных марок и фронтальные погрузчики, используемые для зачистки экскаваторных забоев и выравнивания поверхности отвалов. Для строительства дорог применяют тяжелые бульдозеры, скреперы, грейдеры и фронтальные погрузчики.
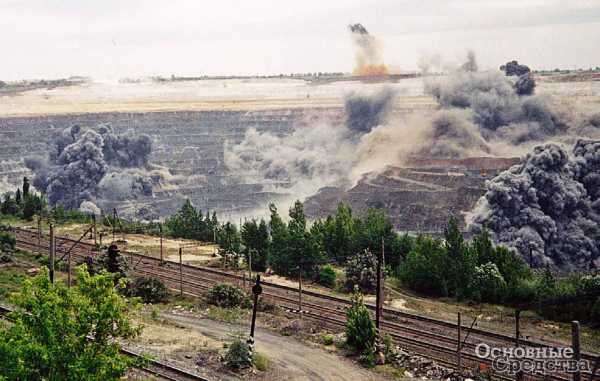
Погрузочная техника должна быть соизмерима с самосвальной – этот фактор серьезно влияет на сроки окупаемости самосвала, которые напрямую зависят от интенсивности его транспортной работы. Увеличенное время погрузки отрицательно сказывается на производительности машин. На Лебединском ГОКе самосвалы заполняют рудой с помощью тросовых электрических экскаваторов производства АО «Ижорские заводы». Вместимость ковшей «прямая лопата» экскаваторов моделей ЭКГ-8Ш, ЭКГ-10 и ЭКГ-12,5 соответственно 8, 10 и 12,5 м3. Это позволяет заполнить кузов автомобиля за 6…8 циклов, что не всегда является оптимальным. К сожалению, попытка поднять производительность за счет использования некоторое время назад двух ижорских 15-кубовых экскаваторов не дала положительных результатов: они не были приспособлены для работы с твердыми скальными породами.
Использование на Лебединском ГОКе самосвалов грузоподъемностью 120…130 т помимо сказанного вызвано нарастанием глубины карьера, а следовательно, и плеча откатки. Максимальная производительность достигается за счет круглосуточной работы экскаваторов и самосвалов, за исключением случаев, когда требуется профилактическое обслуживание или ремонт. За смену самосвалы вывозят 40 тыс. т руды и 5…6 тыс. кубометров вскрышных пород. За сутки транспортируется 120 тыс. т горной массы. Например, среднемесячная выработка на один БелАЗ-75131 составляет 147 тыс. т, пробег с грузом достигает 18 000 км, грузооборот – 1720 тыс. т·км. За каждым самосвалом закреплен экипаж из четырех человек. Рабочая смена каждого водителя длится по 12 ч.
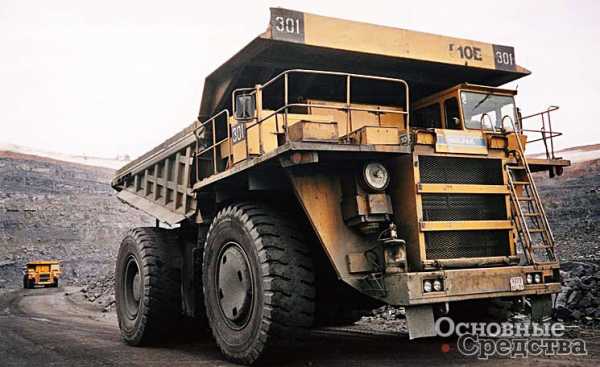
Лучшие эксплуатационные характеристики показывают самосвалы Haulpak 510Е, по конструктивным решениям и качеству изготовления превосходящие и БелАЗы, и Komatsu. Например, наработка до капремонта японской машины – 18…19 тыс. ч, а у американца – 30 тыс. ч. Годовая наработка БелАЗ – 6,5 тыс. ч, а Haulpak (из-за меньших простоев) – 7,5 тыс. ч. Надежность работы самосвалов, как показывает практика, в первую очередь зависит от двигателя. В свое время большие проблемы создавали словацкие дизели Pielstick на БелАЗах модели 75191: половина всех отказов приходилась именно на этот агрегат. Сегодня все самосвалы грузоподъемностью 120…130 т, эксплуатируемые на Лебединском ГОКе, оборудованы американскими V-образными 16-цилиндровыми дизелями Cummins моделей КТА38 и КТА-50 мощностью 1200 и 1500 л.с. соответственно. К сожалению, отечественные моторостроители еще не могут предложить конкурентоспособные модели в этом диапазоне мощности. Дизель серии 8ДМ-21, выпускаемый в России, также уступает зарубежным аналогам.
Отметим, что по сравнению с предыдущими моделями самосвалов БелАЗ-75131 оснащен более надежным генератором переменного тока СГДУ, изготовленным в Екатеринбурге. У этих агрегатов за два года работы произошел только один отказ. Усовершенствованы и мотор-колеса. Ресурс колесного планетарного редуктора, к сожалению, не более 8 месяцев, после чего его надо ремонтировать. Требуют решения вопросы, касающиеся тяговых электродвигателей. Применяемые ранее электромоторы ИК-420 и ИК-420А, производимые в Татарстане, оказались ненадежными – уже в первые месяцы работы стали выходить из строя коллекторы. Пришлось попросить БелАЗ перейти на аналогичные агрегаты ТЭД 6 (С.-Петербург), однако и у них есть изъяны.
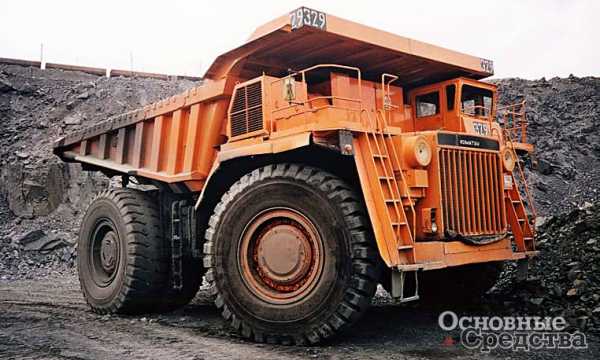
В карьерных самосвалах в отличие от классических используется подвеска с пневмогидравлическими упругими элементами и встроенным регулятором жесткости. Нелинейная упругая характеристика подвески обеспечивает необходимую плавность хода самосвала в груженом и порожнем состоянии. На всех автомобилях применяется гидравлическое управление, особенность которого – наличие гидроаккумулятора, обеспечивающего работоспособность рулевого управления при выходе из строя насоса или двигателя самосвала. Передние колеса поворачивают два силовых гидроцилиндра двустороннего действия, дозированную подачу рабочей жидкости в которые обеспечивает следящая система. Гидросистема рулевого управления объединена с гидросистемами подъема кузова и тормозной системой. Хорошим подспорьем на БелАЗах и Haulpak является система централизованной смазки подшипников рулевых тяг и реактивных штанг Lincoln.
Для обеспечения безопасности карьерные самосвалы оборудованы четырьмя тормозными системами – рабочей, вспомогательной, стояночной, запасной (аварийной). На машинах с полезной нагрузкой 120…130 т нашел применение гидравлический привод. Рабочие и запасные тормозные системы самосвалов выполнены с раздельным приводом для передних и задних колес. Для каждого из контуров предусмотрены отдельные аварийные гидроаккумуляторы. Нормальная работа тормозной системы карьерного самосвала возможна лишь при наличии вспомогательной тормозной системы, которая обеспечивает замедленное движение грузовика под уклон и разгружает основную рабочую систему.
У автомобилей с электрической трансмиссией применяется так называемая динамическая система. При нажатии на тормозную педаль сначала срабатывает динамическая система, а затем – рабочая. В качестве рабочих установлены дисковые тормозные механизмы. Самосвалы Лебединского ГОКа оснащены специальными шинами, у которых меньше вероятность порезов породой. На скальных породах лучше себя показали французские шины Michelin и японские Bridgestone с радиальным расположением корда, но и они выдерживают не более 65…70 тыс. км. Каждая такая шина стоит около 10 тыс. USD. От диагональных шин, выпускаемых в Бобруйске, отказались из-за их низкой надежности и долговечности.
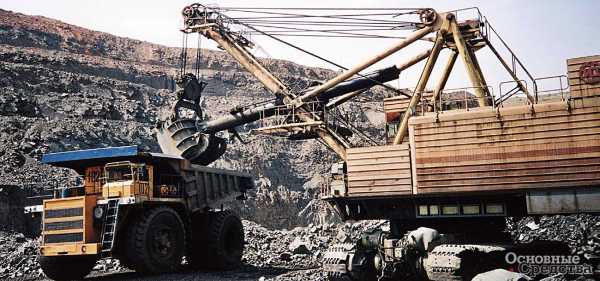
Облегчает работу и обслуживание карьерных самосвалов Haulpak комплексная электронная система диагностирования. Она контролирует множество параметров работы автомобиля, предупреждая водителя о неисправностях. Система автоматического взвешивания груза на Haulpak и БелАЗах обеспечивает равномерную загрузку, повышая производительность и срок службы самосвалов. В недалеком будущем на БелАЗах появятся устройства контроля давления воздуха в шинах и количества топлива в баках. Такие машины станут трудиться и на Лебединском ГОКе. В кабине самосвала находятся медицинская аптечка, огнетушитель, при необходимости выдается респиратор. БелАЗы, Haulpak и Komatsu из последней партии оснащены кондиционерами и системами пожаротушения, управляемыми вручную.
Наиболее комфортные условия для работы водителя, по общему мнению, созданы на БелАЗ-75131. К услугам шофера – просторная кабина с термо-, шумо- и виброизоляцией, высокопроизводительные системы отопления и вентиляции, кондиционер, информативная панель приборов, удобно расположенные органы управления, регулируемые рулевое колесо и сиденье на индивидуальной пневматической подвеске. Кабина оснащена защитой ROPS от опрокидывания.
Нельзя не упомянуть о рекордсмене. В цехе технологических машин с 1980 г. эксплуатируется самосвал Komatsu HD1200, пробег которого превысил 1 млн. км, или примерно свыше 100 тыс. машино-ч. Сейчас этот образец собственными силами переоборудовали в 60-кубовую поливочно-оросительную машину. Такая техника нужна для того, чтобы постоянно увлажнять внутрикарьерные дороги и предотвращать пылеобразование, вредное для человека.
os1.ru
Прародитель карьерных самосвалов – Основные средства
А. Краснов
Название Euclid (произносится – «юклид») впервые появилось в 1931 году на облицовке радиаторов тяжелых грузовиков. Так стала называться продукция фирмы Euclid Crane and Hoist Company, основанной с подачи владельцев Euclid Road Machinery. История этой фирмы настолько запутанная, что описать ее в простом повествовании невозможно. Компания зародилась еще в XIX веке и отчасти была связана с некоторыми автопроизводителями северноамериканского континента, а позже Европы и даже Японии. Все события и изменения в ее развитии происходили не одно за другим, а последовательно-параллельно. Именно в таком ключе и нам придется рассказывать о том, как появились тяжелые грузовики с названием Euclid.
Euclid Trac-Truk 1933 г. |
Обе упомянутые компании основали и зарегистрировали пятеро братьев Армингтон в Кливленде, штат Огайо. Первые годы деятельности братья занимались ремонтом и продажей разного рода строительной и сельскохозяйственной техники. В 1930 году, проанализировав рынок, они решили направить все усилия в сферу производства тяжелой автомобильной техники.
Благодаря помощи друзей-конструкторов братья Армингтон разработали и собрали фактически первый в мире карьерный самосвал, т. е. грузовик для решения конкретных задач, а не универсальное шасси, чем в те годы занималось большинство производителей грузовиков во всем мире. Автомобиль выглядел нескладным, но его основные характеристики значительно отличались от существующих аналогичных машин. Кузов был непривычной ковшовой формы с задней разгрузкой, над кабиной водителя – подобие защитного козырька, колеса разного диаметра. Отличительной чертой грузовика была его проходимость. На задних, ведущих колесах были надеты специальные кольца с мощными грунтозацепами. Грузоподъемность первенца около 8 т, кабина водителя не была приспособлена к зимней эксплуатации, не имела дверей, а значит, и отопления.
Euclid 1930 г. |
Именно этот грузовик стал предшественником огромного семейства современных карьерных монстров. Массированная атака на владельцев открытых грунтовых разработок и строительных объектов, где требовалась перевозка больших объемов песка, гравия, камней и т. д., началась годом позже, когда была зарегистрирована фирма. И раньше производили самосвалы с задней и с боковой разгрузкой, но таких, с карьерной направленностью, еще не было.
В 1933 году фирма приступила к мелкосерийному выпуску грузовика с названием Trac-Truk. Новый самосвал мало походил на предшественника. Он отвечал многим требованиям безопасности и комфорта того времени. Не очень удобные грунтозацепы на задних колесах были заменены сдвоенными шинами с крупным протектором, позаимствованным у тогдашних тракторов. Кузов имел своеобразный защитный козырек над кабиной. Для подъема кузова уже применялась гидравлика. Привод осуществлялся на задние колеса, и благодаря относительно небольшой базе и большому углу поворота передних колес маневренность самосвала была очень высокой. Грузоподъемность этой машины составляла 11 т. Ее оснастили полноценной кабиной с дверьми, стеклоочистителями и другими необходимыми для любого грузового автомобиля атрибутами.
Euclid R-35 1980 г. |
В 1936 году компания разработала и запустила в производство совершенно новую модель – 15-тонный самосвал 1FB, избавленный от некоторых недоработок предыдущей модели. Он оказался настолько удачным, что практически без изменений его выпускали вплоть до 1954 года. Несколько раз модернизировали только дизель.
Помимо грузовиков фирма Euclid освоила выпуск погрузчиков, скреперов, другого специального оборудования и техники. В это же время был выпущен оригинальный 20-тонный самосвал, предназначенный специально для перевозки каменного угля. Одним словом, дела предпринимателей шли довольно успешно. Доселе невиданный по масштабам 60-тонный скрепер разработан в 1949 году. В 1951-м выпущен легендарный 45-тонный трехосный самосвал для перевозки породы на открытых разработках. Его оснащали двумя дизелями фирмы Cummins cуммарной мощностью 670 л.с. У этого самосвала, вернее шасси, было несколько модификаций, в том числе седельный тягач с кузовом для перевозки сыпучих грузов.
White-Euclid UC R210 1973 г. |
Именно сейчас надо отступить от прямого повествования и вернуться назад во времени. Известная американская фирма White, выпускающая в основном магистральные тягачи, была основана в 1866 (!) году. Сначала она занималась изготовлением механических узлов для различных машин, даже для станков, а с 1876 года перешла на производство комплектующих для наземного транспорта. В 1900 году White начинает выпуск легковых автомобилей с паровыми двигателями. По окончании Первой мировой войны легковушки были забыты, и фирма занялась грузовыми автомобилями. В этой области она преуспела до такой степени, что начала поглощать обедневшие предприятия близкого профиля. Было приобретено несколько именитых фирм, в том числе Autocar. Помимо привычных грузовиков White выпускала и карьерные самосвалы высокой грузоподъемности – от 65 до 105 т. Так, грузоподъемность трехосного карьерного самосвала Autocar A.P. 40 1958 года составляла 80 т. Его оснащали несколькими видами дизельных двигателей мощностью от 500 до 600 л.с. и 9-ступенчатой коробкой передач.
Уже очень крупный конгломерат White Motor Corp., объединивший около десяти именитых фирм, поглотил и Euclid, испытывающий к тому времени определенные финансовые трудности. Некоторые очень интересные разработки стали носить двойное название – White/Euclid. Производственная программа вновь созданного юридического лица была очень широкой – от тракторов до мощнейших по тем временам скреперов и самосвалов. Под таким двойным названием было построено несколько предприятий в Великобритании (точнее, в Шотландии), Бельгии и Канаде.
Autocar A.P. |
В 1973 году отделение White/Euclid сконструировало двухосный 8-колесный самосвал, на который в качестве двигателя установили газовую турбину мощностью 1850 л.с. Он брал «на борт» 191 т полезного груза и должен был пойти в серию, но сложившиеся неблагоприятные обстоятельства не позволили этого сделать.
Одновременно с White банкротством Euclid заинтересовалась корпорация General Motors, прикупив часть активов «тонущего корабля», благо разработок и идей у Euclid хватало. Эта крупнейшая корпорация также наладила производство на предприятиях Канады и Шотландии. В Европе они были известны под торговой маркой Terex. Грузоподъемность самосвалов этой компании была небольшая – всего 15…20 т, в качестве силовых агрегатов использовались двигатели Rolls-Royce.
С 1968-го по 1972 год корпорация General Motors и фирма White конкурировали между собой, но ситуация выглядела несколько гротескно: некоторые грузовики назывались White/Euclid, а некоторые – GM/Euclid. Такое положение неблагоприятно сказывалось на продажах продукции.
GM-Euclid LLD Eucnick 1958 г. |
При этом фирма Euclid продолжала заниматься и собственными разработками, только в меньших масштабах. Так, по заданию Пентагона она разрабатывала армейские машины, но была и тяжелая гражданская техника. Например, в 1969 году фирма разработала самосвал грузоподъемностью 110 т.
Трехосное шасси LLD, упомянутое выше, с кузовом ковшового типа, установленным на полуприцепе, называлось GM-EUСNICK. Седельный тягач грузоподъемностью 120 т оснащали двухосным полуприцепом, а приводился в движение он двумя дизелями мощностью по 375 л.с. каждый.
Euclid также построила в 1974 году седельный тягач для перевозки сверхтяжелых и негабаритных грузов. Нагрузка на седло равнялась 290 т. Примерно в это же время GM/Euclid выпускает оригинальный скрепер SS-40 длиной 52 м (!), грузоподъемностью 160 т. Эти тонны заполняют ковши скрепера всего за 2 минуты. Правда, в этом им помогает 2200-сильный двигатель тягача.
Euclid R-35 1977 г. |
Иногда GM позволял себе «небольшие» эксперименты. В начале 1970-х, например, выпущен полноприводный двухосный самосвал Euc-RX со сдвоенными передними и задними колесами. Его грузоподъемность составляла 156 т.
В 1977 году германский концерн Daimler-Benz приобрел немало американских фирм самого разного профиля, производящих разнообразную технику, от тракторов до дорожных машин. В этот список приобретений попали и все предприятия Euclid. Именно с этого времени стали выпускать карьерные самосвалы разной грузоподъемности, но с одним дизайнерским стилем, который сохранился по сей день. Это грузовики серии R, которые уже были заложены в программе White/Euclid. Серия, доработанная в составе концерна Daimler-Benz, отличается хорошим внешним видом, очень качественно отработанным интерьером кабины водителя и фирменной, салатного цвета, заводской окраской.
Euclid S-18 |
Заводы Euclid не исчезли, они остались в США, кроме того, их стало больше в Канаде (заводы VME). Последние два десятка лет они плотно сотрудничали с Hitachi Heavy Eqipment. После объединения Daimler-Benz и Chrysler предприятия перешли в собственность компании DaimlerChrysler, а в начале 2004 года Euclid была полностью приобретена фирмой Hitachi Construction Truck Manufacturing. Ради этого Hitachi даже поменяла свое название.
Нельзя не отметить еще раз, что история Euclid сложна и многогранна. Она изобилует неожиданными поворотами и возвратами, сотрудничеством с разными фирмами и разрывом деловых отношений. За все время существования компания выпустила более 44 000 карьерных самосвалов, не считая скреперов и другой тяжелой техники. Конструкторы этого интересного коллектива разработали десятки уникальных машин, среди которых надо упомянуть GM-Terex Titan, но этот грузовик заслуживает отдельного рассказа.
os1.ru