Устройство кузова полувагона. — Студопедия.Нет
СОДЕРЖАНИЕ
Стр. | ||
Введение. | 3 | |
1. | Конструкция четырехосного полувагона с глухим кузовом | 5 |
1.1. | Устройство кузова полувагона | 5 |
1.1.1. | Боковая стена полувагона | 5 |
1.1.2. | Торцевая стена полувагона | 6 |
1.1.3. | Рама полувагона | 7 |
1.2. | Ходовая часть | 10 |
1.3. | Автосцепное устройство | 12 |
1.4. | Расцепной привод, ударно-центрирующий прибор, упряжное устройство и опорные части | |
1.5. | Поглощающий аппарат | 14 |
1.6. | Тормозное оборудование | 16 |
2. | Основные параметры грузового вагона | 18 |
2.1. | Расчет технико-экономических параметров вагона | 18 |
3. | Расчет несущих конструкций кузова | 23 |
3.1. | Расчет прочности кузова вагона | 23 |
3.2. | Уточненный расчет рамы полувагона на продольную нагрузку по МКЭ | 25 |
4. | Оценка соответствия ходовых качеств вагона требованиям «Норм» | 27 |
4.1. | Коэффициенты динамики и амплитуды ускорений | 27 |
4.2. | Показатели плавности хода | 29 |
4.3. | Коэффициент запаса устойчивости колеса от вкатывания на головку рельса | 29 |
4.4. | Валкость кузова | 32 |
5. | Расчеты прочности элементов ходовых частей | 34 |
5.1. | Боковая рама тележки | 34 |
5.2. | Колесо и ось | 37 |
5.3. | Буксовый узел | 38 |
6. | Оценка соответствия требованиям «Норм» элементов ударно-тяговых устройств | 40 |
6.1. | Проверка автоматической сцепляемости вагона | 40 |
6.2. | Проверка прохода вагоном сортировочных горок и аппарелей паромных переправ | 41 |
7. | Дополнительные оценки безопасности движения вагона, предусмотренные «Нормами» | 42 |
7.1. | Устойчивость от выжимания продольными силами | 42 |
7.2. | Устойчивость вагона от опрокидывания наружу кривой | 43 |
Список литературы | 45 | |
Графическая часть | ||
А1 | Четырехосный полувагон с глухим кузовом (Общий вид) |
Введение.
Общие закономерности циклического развития экономики отражаются в начавшемся с 1989 года сокращении объема перевозок на железных дорогах России. Но рост спроса на транспортном рынке в процессе стабилизации экономики и особенно в начале ее подъема также будет интенсивным. Вагонный парк должен быть подготовлен к этому времени заблаговременно.
В бывшем СССР грузовые вагоны выпускали семь заводов России и четыре Украины. Суммарная мощность этих заводов на 1.01.91 года составляла 73,12 тысяч единиц в год, из которых на Россию приходилось 48,5%, Украину – 51,5%. При этом действовала внутриотраслевая кооперация вагоностроительных заводов и сложившаяся система поставки комплектующих частей, полуфабрикатов, материалов.
После распада СССР в ближайшие годы необходимо создать новую схему размещения производства вагонов в России, организовать более гибкую специализацию действующих и создающихся мощностей, обеспечить наращивание производственных мощностей до уровня, определяемого потребностями народного хозяйства. Важно предусмотреть такое развитие вагоностроения, при котором потребности железнодорожного транспорта будут обеспечиваться отечественными предприятиями. Роль железных дорог в России очень велика, чтобы допустить стратегическую зависимость народного хозяйства от поставок подвижного состава из других стран.
Однако, имеющихся действующих мощностей недостаточно для удовлетворения потребностей железнодорожного транспорта. В этих условиях целесообразно создавать новые рабочие места на территории России, перепрофилировать на выпуск подвижного состава предприятий специального назначения. Важно и то, что при активном развитии отечественного производства и вагоностроения создаются наиболее благоприятные условия для изготовления запасных частей (на тех же мощностях), облегчается возможность сервисного обслуживания вагонов.
Вагоны отечественного производства значительно дешевле импортных. Цена нового современного грузового вагона в США, в зависимости от типа, колеблется от 72 тысяч до 40 тысяч долларов, что в 2,5-3 раза больше, чем цена наших вагонов. Суровые климатические условия российских железных дорог предъявляют повышенные требования к качеству металла и других материалов при температуре окружающего воздуха до -60 0С. в других странах, даже в Канаде, такой проблемы не существует.
Основные направления развития конструкции и параметров грузовых вагонов железных дорог России на среднесуточную перспективу представляются следующими: освоение нового поколения четырехосных вагонов с осевой нагрузкой брутто до 24,5-25,0 кН, погонной нагрузкой на путь 8-8,3 т/мп, увеличенными габаритными размерами, обеспечивающими более высокие грузоподъемность и вместимость, дальнейшее расширение парка специализированных вагонов при рациональном выборе степени специализации, которая должна обеспечить повышение качества перевозок, снизить трудоемкости и стоимости погрузочно-разгрузочных работ, сокращение, вплоть до полной ликвидации, потерь грузов и загрязнения окружающей среды, ужесточение требований к прочности, износостойкости и надежности узлов и элементов вагонов, снижение трудоемкости и стоимости ремонта, повышение безопасности движения.
В настоящее время назрела необходимость в новой системе производства грузовых вагонов на предприятиях России. Нужна максимальная, гибкая технология производства, особенно в заготовительных и сборочно-сварочных цехах и участках. Это должно помочь заводам переходить на выпуск новых моделей вагонов, быстро реагировать на изменение спроса и потребностей железнодорожного и промышленного транспорта.
С учетом имеющихся мощностей вагоностроительных предприятий России и их развития, намечаемого проектом Федеральной программы, в ближайшие годы можно ожидать освоения производства нескольких новых типов грузовых вагонов: платформы длиной 19,6 м; крытых вагонов для двухъярусной перевозки автомобилей; вагонов со съемной крышей для рулонной стали; вагоны-цистерны для перевозки нефтебензиновых грузов, цемента; вагонов-самосвалов шестиосных с грузоподъемностью 105 т, а также работы по усовершенствованию предыдущих моделей грузовых вагонов, например, четырехосных полувагонов, цельнометаллических с глухим кузовом и полом с повышенными осевой и погонными нагрузками.
1. Конструкция четырехосного полувагона с глухим кузовом.
Парк вагонов на железных дорогах СНГ состоит из нескольких миллионов единиц подвижного состава. Среди них 2,5 миллиона приходится на грузовые составы, остальные, около 700-800 тысяч единиц – на пассажирские. В составе грузового парка вагонов находятся различные типы конструкций вагонов: полувагоны, крытые вагоны, цистерны, платформы, хоппера, рефрежераторные вагоны, универсальные вагоны, а так же специализированные – для перевозки автомобилей, зерновозы, цементовозы. В перечисленном парке преобладают полувагоны. На их долю приходится 50% от состава грузового парка вагонов.
Полувагоны предназначены для перевозки каменного угля, руды, леса, проката, металлов, строительных материалов, а так же других сыпучих и штучных грузов, не требующих защиты от атмосферных осадков. По числу осей полувагоны бывают четырех-шести-, и восьмиосными. Применяются два основных типа полувагонов: с торцевыми, открывающимися внутрь вагона дверями и разгрузочными люками в полу, другой же тип представляет рассматриваемая модель четырехосного полувагона с глухим кузовом, то есть без дверей и разгрузочных люков в полу. Такие модели полувагонов используются в основном для перевозки только сыпучих грузов в замкнутых маршрутах с разгрузкой на вагоноопрокидывателях.
Конструкция полувагона состоит из следующих основных узлов: цельнометаллического кузова вагона; ходовых частей, состоящих из двух двухосных тележек модели 18-100 ГОСТ 9246-79; ударно-тяговых приборов, включающих в себя автосцепку типа СА-3, поглощающий аппарат Ш2В и тяговый хомут с клином.
Устройство кузова полувагона.
Кузов полувагона предназначен для размещения и перевозки всех грузов, не требующих укрытия от атмосферных осадков, как насыпных пылевидных, так и навалочных (за исключением горячих с температурой более 100 оС), штучных, с креплением их в соответствии с требованиями правил погрузки, а также для передачи продольных сжимающих или растягивающих усилий, возникающих при движении поезда.
Кузов полувагона состоит из следующих составных частей: двух боковых стен, двух торцевых стен, рамы.
1.1.1. Боковая стена кузова полувагона (рис. 1.1.1.) состоит из стоечносварной конструкции, представляющей собой каркас и металлическую обшивку. Боковая стена является основным несущим элементом конструкции кузова, выполненной из стали 09Г2. Боковые стены кузова воспринимают вертикальные нагрузки, распорные и динамические нагрузки, действующие на полувагон при эксплуатации.
Рис. 1.1.1. Боковая стена полувагона.
Каркас боковой стены состоит из верхней 2 и нижней 5 обвязок, соединенных между собой угловыми стойками 1, шкворневыми 4 и промежуточными 3. К каркасу боковой стены приварена обшивка 6.
Верхняя обвязка предназначена для восприятия эксплуатационных нагрузок, а также нагрузок, возникающих при разгрузке вагонов на вагоноопрокидывателях. Обвязка выполнена из холодногнутого уголка 155×10×6 по ТУ-12-2-341-78 и горячекатаного по ГОСТ 5267.14-78.
Соединенные между собой сваркой, профили верхней обвязки образуют жесткую коробчатую конструкцию. Для увеличения жесткости внутри верхней обвязки установлены ребра.
Нижняя обвязка выполнена из уголка 160×100×10 ГОСТ 8510-86 и предназначена для соединения боковой стены с рамой полувагона и для соединения заделки промежуточных стоек с балками рамы.
Угловые стойки выполнены из листа и предназначены для соединения боковых и торцевых стен с рамой.
Промежуточные стойки предназначены для восприятия распорных усилий, возникающих при перевозке сыпучих грузов, соединение боковой стены с рамой полувагона представляет собой омегообразный профиль, изготовленный горячей каткой.
Обшивка изготовляется из двух периодических профилей проката по ТУ-14-2-210-77 толщиной 3,6 и 4,5 мм, соединенных внахлестку по высоте.
С внутренней стороны, для возможности осмотра и очистки кузова от груза, по диагонали расположены в полу люки.
1.1.2. Торцевая стена кузова полувагона (рис. 1.1.2.) предназначена для восприятия распорных нагрузок от действия сыпучих грузов, а также продольных инерционных, действующих на полувагон в эксплуатации.
Рис. 1.1.2. Торцевая стена полувагона.
Торцевая стена включает в себя верхнюю 1 и нижнюю 6 обвязки; два горизонтальных пояса 2; стойки 3; усиливающие стойки 5; листы обшивки 4 и 7. Горизонтальные пояса выполнены из горячекатаного проката по ТУ-14-1-2220-77, как и промежуточные стойки боковой стены и расположены параллельно верхней и нижней обвязкам по всей ширине стены.
Верхняя обвязка выполнена из холодного швеллера 144×160×90×6 мм по ГОСТ 8281-80 с усилением его планкой для создания жесткой коробчатой конструкции.
Нижняя обвязка выполнена из уголка 160×100×10 мм ГОСТ 8510-86 и предназначена для соединения торцевой стены с рамой.
Стойки выполнены из горячекатаного швеллера 12 ГОСТ 8240-72 и обеспечивают соединение торцевой стены с угловой стойкой.
Усиливающие стойки выполнены из штампованного П-образного сечения 144×90×6 и предназначены для усиления заделки торцевой стены с рамой.
Обшивка торцевой стены по ТУ-14-2-280-77 толщиной 5 мм выполнена из двух гладких листов, соединенных между собой по высоте внахлестку.
Все элементы торцевой стены соединены между собой с помощью электродуговой сварки.
1.1.3. Рама полувагона (рис. 1.1.3.1.) является одной из ответственных частей полувагона, служит основанием кузова и воспринимает вертикальную нагрузку от груза, собственного веса и веса кузова, а также ударные усилия – растягивающие и сжимающие. Через пятники на шкворневых балках рама опирается на надрессорные балки тележек. В центральные отверстия пятников и подпятников вставлены шкворни. На раме устанавливается автосцепное устройство, тормоз полувагона.
Рис.1.1.3.1. Рама полувагона.
Рама полувагона состоит из хребтовой балки 1, двух концевых балок 2, двух шкворневых 3, четырех промежуточных 4 и 5.
В средней части рамы размещены: кронштейн для тормозного оборудования, то есть тормозного цилиндра 6, кронштейн для крепления камеры 7 и угольника для крепления запасного резервуара 8. На одной из концевых балок установлен поручень сцепщика.
Хребтовая балка(рис. 1.1.3.2) воспринимает вертикальные, растягивающие, сжимающие и ударные нагрузки и предназначена для размещения автосцепного устройства и крепления кронштейнов тормозного оборудования. Она состоит из двух зетов 1 высотой 310 мм. Расстояние между вертикальными стенками внутри хребтовой балки равно 350 мм. По концам хребтовой балки расположены передние и задние упоры 4. В узле соединения хребтовой балки с шкворневыми балками установлены подпятниковые коробки 5, которые усиливают место под пятником и связывают между собой вертикальные стенки хребтовой балки. В районе установки промежуточных балок, в хребтовую балку вварены нижние листы 6 и ребро жесткости 3.
Рис. 1.1.3.2. Хребтовая балка.
Концевая балка (рис. 1.1.3.3.) представляет собой сварную конструкцию, состоящую из верхнего листа 1, лобового листа 2, двух нижних листов 4, двух листов уплотнения 3. Средняя часть листа углублена по отношению к концу на 16 мм.
Концевая балка полувагона предназначена для восприятия нагрузки от всех видов перевозимых грузов, а так же для крепления и установки торцевой стены.
Рис. 1.1.3.3. Концевая балка.
По вершинам между лобовым листом, нижним и листом уплотнения установлены ребра жесткости. На лобовом листе устанавливается поручень сцепщика 7, кронштейн расцепного привода 5 и скобы для сигнального фонаря. К нижним листам снизу приварены листы для поддомкрачивания 6.
Шкворневая балка (рис. 1.1.3.4.) предназначена для передачи через пятники и скользуны на тележку всех, возникающих в процессе движения полувагона, статических и динамических усилий.
Рис. 1.1.3.4. Шкворневая балка.
Она представляет собой конструкцию коробчатого сечения переменной высоты с верхним корытообразной формы листом, двумя вертикальными листами и нижним листом. К нижнему листу приварены скользуны. Между вертикальными листами для жесткости установлены диафрагмы. К нижнему листу, зетам и подпятниковой коробке крепится пятник.
Соединение шкворневой балки со шкворневыми стойками боковой стены осуществляется посредством накладок.
Промежуточные балки предназначены для соединения боковой стены с рамой полувагона, они воспринимают часть нагрузок, действующих на раму. Балки представляют собой сварную конструкцию двутаврового сечения переменной высоты, состоящих из вертикальных листов, нижних листов и верхнего листа, имеющего корытообразную форму (рис. 1.1.3.5.).
Рис.1.1.3.5. Промежуточная балка.
Соединение балок со стойками боковой стены осуществляется с помощью накладок.
Ходовая часть
В настоящее время грузовые вагоны железных дорог России строят с тележками типа 18-100 (рис.1.2), которые имеют клиновые гасители колебаний.
Боковая рама 3 тележки выполнена в виде стальной отливки, в средней части которой расположен проем для рессорного комплекта, а по концам — проемы для букс.
В верхней части буксовых проемов имеются кольцевые приливы, которыми боковые рамы опираются на буксы, а по бокам — буксовые челюсти.
Сечения наклонных элементов (поясов) и вертикальных стержней (колонок) боковой рамы имеют корытообразную форму с некоторым загибом внутрь концов полок. Горизонтальный участок нижнего пояса имеет замкнутое коробчатое сечение. Балки с таким профилем хорошо сопротивляются изгибу и кручению.
По бокам среднего проема в верхней части рамы расположены направляющие для ограничения поперечного перемещения фрикционных клиньев, а внизу имеется опорная поверхность для установки рессорного комплекта. С внутренней стороны к этой поверхности примыкают полки, являющиеся опорами для наконечников триангелей в случае обрыва подвесок, которыми триангели подвешены к кронштейнам боковой рамы.) В местах расположения клиньев к колонкам рамы приклепаны фрикционные планки. На наклонном поясе отливают пять цилиндрических выступов (шишек), часть которых срубается в соответствии с, фактическим расстоянием между наружными челюстями буксовых проемов. Подбор боковых рам при сборке тележек производят по числу оставленных шишек, что гарантирует соблюдение необходимых допусков для обеспечения параллельности осей колесных пар.
Надрессорная балка тележки отлита заодно с подпятником, опорами для размещения скользунов, гнездами для фрикционных клиньев и приливом для крепления кронштейна мертвой точки рычажной передачи тормоза. Балка выполнена по форме бруса равного сопротивления изгибу в соответствии с эпюрой изгибающих моментов и имеет коробчатое замкнутое сечение.
Рис.1.2 Тележка 18-100.
Автосцепное устройство
Автосцепное устройство вагона обычно состоит из следующих частей: корпуса и расположенного в нем механизма; расцепного привода; ударно-центрирующего прибора; упряжного устройства; поглощающего аппарата; опорных частей.
Устройство корпуса и механизма автосцепки определяет ее тип и конструкцию, поэтому корпус с механизмом часто называют автосцепкой.
Вагоны и локомотивы магистральных железных дорог Советского Союза оборудованы автоматической сцепкой СА-3 (советская автосцепка, третий вариант), утвержденной в 1934 г. в качестве типовой. Эта автосцепка (рис. 1.3) относится к нежестким.
Рис.1.3 Корпус автосцепки СА-3.
studopedia.net
Назначение и конструкции полувагонов
содержание .. 19 20 21 ..
7.4.
Назначение и конструкции полувагонов — часть 1
Полувагон — наиболее универсальный тип вагона. Он предназначен для перевозки угля, руды, щебня, леса, металлопроката, а также других сыпучих (не пылевидных) и штучных грузов, не требующих защиты от атмосферных осадков. Полувагоны характеризуются самой высокой степенью использования на магистральном и промышленном транспорте. Перевозки таких грузов, как уголь и руда от мест добычи к потребителям осуществляются только полувагонами.
Как известно, четкая и ритмичная работа ключевых отраслей экономики страны во многом зависит от своевременной доставки на предприятия угля и руды. Ежесуточная производительность полувагонов более чем в два раза превышает производительность других типов вагонов. Полувагоны обеспечивают около 70% объема перевозок, осуществляемых железнодорожным транспортом.
Универсальный полувагон имеет открытый сверху кузов (нет крыши), благодаря чему можно механизировать погрузочные работы с помощью экскаваторов, кранов, конвейеров и других погрузочных устройств. Выгрузка сыпучих грузов механизированным спо-собом осуществляется на вагоноопро-кидывателях. Полувагоны разделяются по осности на четырех-, шести- и восьмиосные.
Четырехосный цельнометаллический полувагон (рис. 7. 11)
грузоподъемностью 63 т с объемом кузова 72,5 м3 выпускается серийно
Крюковским вагоностроительным заводом с 1969 г.
Рама полувагона (рис. 7. 12) представляет собой цельносварную конст-рукцию, состоящую из хребтовой 4; концевых 5, шкворневых 3, промежуточных 2 и средних 1 балок.
Рис. 7.12. Рама четырехосного цельнометаллического полувагона.
Рис. 7.13. Боковая стена четырехосного цельнометаллического полувагона.
Хребтовая балка является основным несущим элементом рамы и образована двумя балками зетового профиля № 31 и балкой двутаврового профиля № 19. К вертикальным стенкам зетов (расстояние между ними равно 350 мм по концам их приклепаны передние и задние упоры автосцепного устройства. Концевая балка сварена из штампованного угло-. вого профиля и нижнего листа, имеющих толщину 7 мм. Шкворневая балка коробчатого сечения изготавливает-: ся из двух вертикальных, верхнего и нижнего горизонтальных листов толщиной соответственно 8, 10 и 12 мм. В зоне пересечения хребтовой и шкворневых балок устанавливаются усиливающие надпятники, а к нижним листам шкворневых балок приклепаны пятники диаметром 300 мм и приварены скользуны. Промежуточные и средние балки сварены каждая в виде двутавра из вертикального, верхнего и нижнего листов, имеющих толщину соответственно 7, 8 и 12 мм. Все поперечные балки выполнены с переменным по длине сечением.
Кузов полувагона цельнометаллический, сварной конструкции, состоит из
двух боковых стен и двух торцовых дверей со створками (см. рис. 7. 11),
открывающимися внутрь вагона. Боковая стена (рис. 7. 13) включает в себя
верхний 5 и нижний 9 обвязочные пояса, две угловые 1 и 8, две шкворневые
2 и четыре промежуточные 3 стойки, а также верхний 4 и нижний 6 листы
обшивки. К листам обшивки снаружи приклепаны ступеньки-лестницы 7.
Внутренние поверхности боковых стен оборудуются увязочными устройствами
для закрепления перевозимых грузов,
а также скобами для установки лесных стоек.
Верхний обвязочный пояс выполнен из гнутого профиля толщиной 6 мм, нижний — из прокатного уголка (160Х X100Х9 мм), шкворневые и промежуточные стойки — из омегообразного специального проката. Расстояния между стойками равны расстояниям между соответствующими поперечными балками рамы полувагона.
Верхний лист обшивки толщиной
4 мм имеет два сплошных по длине гофра, нижний лист толщиной 5 мм имеет один гофр. Гофры листов обращены выпуклостью внутрь кузова. В последнее время Крюковский вагоно-строительный завод выпускает цельнометаллические полувагоны (рис. 7. 14), верхний лист обшивки которых имеет прерывистые по длине гофры с выпуклостью наружу вагона. Нижний лист обшивки не гофрирован. Объем кузова такого полувагона 73 м3.
Каждая створка торцовой двери состоит из каркаса и обшивки в виде гофрированного листа толщиной 4 мм. В закрытом положении двери фиксируются верхним клиновым и нижним запорами.
Пол кузова полувагона образуют 14 крышек разгрузочных люков. К р ы ш-ка
люка (рис. 7.15) представляет собой шестигофровый лист 6 толщиной 5 мм,
подкрепленный двумя боковыми 5, передней 1, надпетельной 4 и средней 2
балочками в виде гнутых или штампованных профилей. К листу и
надпетельной балке приклепаны три
петли 3. С помощью петель и валиков крышки люков шарнирно соединяются с
державками (ушками) двутавра хребтовой балки. Державки крепятся к
вертикальной стенке двутавра с помощью заклепок. В передней части крышки
приклепаны два литых запорных кронштейна 7, которые с помощью типового
запорного устройства удерживают крышку в закрытом (горизонтальном)
положении.
Типовое запорное устройство (рис. 7.16) крышки люка состоит из
запора-закидки 3, скобы 1 и запорного сектора 2. Скоба болтами
прикреплена к нижнему обвязочному поясу боковой стены кузова. Закидка и
сектор насажены шарнирно на болты скобы. В нижней части закидки имеются
два выступа (зуба), которыми она при закрывании крышки последовательно
зацепляется за запорный кронштейн. Верхний выступ служит для плотного
прижатия крышки к нижнему обвязочному поясу, хребтовой и двум поперечным
балкам рамы. Стабильное прижатие закидки к запорному кронштейну крышки
обеспечивается занорным сектором. Естественно, что каждая крышка люка
имеет два запорных устройства. В опущенном состоянии (при разгрузке
вагона) крышки люков опираются на приваренные к поперечным балкам рамы
специальные опоры и образуют угол к горизонтали в средней части 31и, а
над тележками 23°3(У. Крышки оборудованы торсионными устройствами для
облегчения их подъема при закрывании. Один конец торсиона опирается на
раму полувагона, а другой закрепляется на крышке люка. При открывании
крышки торсион закручивается (в пределах упругих деформаций) и стремится
возвратить крышку в закрытое положение. Жесткость торсиона обеспечивает
подъем крышки и установку запорного кронштейна се на нижний выступ
закидки усилием не более 250 Н.
Рис. 7.15. Крышка разгрузочного люка полувагона.
Крышки разгрузочных люков четырех-, шести- и восьмиосных полувагонов взаимозаменяемы. Иными словами, этот элемент конструкции полувагона унифицирован.
Четырехосные цельнометаллические полувагоны грузоподъемностью 63 т с
объемом кузова 73 м3 серийно строят-
ся также Уральским вагоностроительным заводом. Эти полувагоны по
сравнению с полувагонами Крюковского завода имеют только отдельные
непринципиальные отличия в конструкции кузова, связанные с различной
технологией производства: сварка кузова и крышек люков точечная, обшивка
боковых стен в виде отдельных корытообразных выштамповок (панелей) на
Уральском вагоностроительном заводе; сварка кузова и крышек люков
дуговая, обшивка с продольными гофрами на Крюковском заводе.
содержание .. 19 20 21 ..
zinref.ru
3.1.3 Особенности конструкции кузова полувагона |
На примере вагона повышенной до 125 т грузоподъемности рассмотрим конструкцию кузова универсального восьмиосного полувагона модели 12-124 (рис. 3.3) Уральского вагоностроительного завода. Он не имеет крыши, но снабжен разгрузочными люками в полу. По концам кузов оборудован двухстворчатыми открывающимися внутрь дверями.
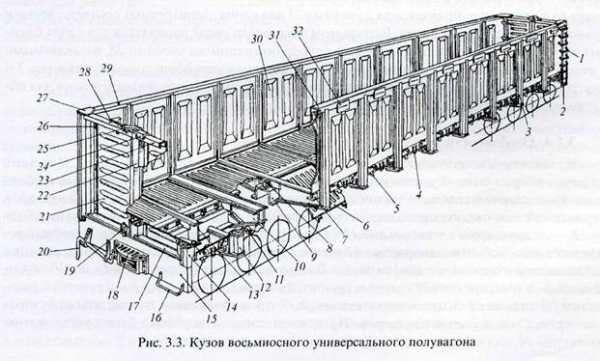
В консольной части хребтовой балки установлены передние и задние упоры автосцепки. Передний упор отлит как одно целое с ударной розеткой 18. Шкворневые балки 10 замкнутого коробчатого сечения снизу имеют пятники и скользуны. Надпятниковые зоны опорных узлов усилены коробками, а над скользунами установлены усиливающие ребра. Сверху к балкам 75 рамы приварены пороги 17, ограничивающие открывание створок дверей наружу кузова.
На торцовых поверхностях концевой балки укреплены рычаг расцепного привода 20 автосцепки и поручень составителя 16. Поперечные балки 13 рамы — двутаврового сечения, верхние их полки имеют гофры, выступающие над уровнем пола, что предупреждает непосредственное опирание длинномерных грузов на крышки разгрузочных люков и предохраняет их от деформации. Подобные выступающие части имеют шкворневые балки 10. Крышки 6 люков гофрированные, снабжены специальными запорами 5, удерживающими их в горизонтальном положении. Крышки также оборудованы торсионными устройствами, облегчающими их подъем при закрывании. Для обеспечения плотного прижатия с помощью рычага крышек на нижней обвязке 7 имеются скобы 4.
Боковые стены кузова имеют металлическую обшивку 30 с корытообразными выштамповками, подкрепленную каркасом, состоящим из верхней 31 и нижней 7 обвязок, а также угловых 14, шкворневых 3 и промежуточных 12 стоек. Шкворневые и промежуточные стойки замкнутого поперечного сечения сварены из Ω-образных профилей. Угловые стойки 14 (замкнутого поперечного сечения) сварены из двух Z-образных элементов, укрепленных к верхней обвязке накладками 27. Верхняя обвязка 31 между стойками усилена накладками 32. Обшивка 30 укреплена к каркасу точечной сваркой.
Двухстворчатые двери шарнирно соединены с угловыми стойками кузова при помощи петель 26. Каждая створка двери состоит из металлической гофрированной обшивки 21, подкрепленной каркасом, состоящим из верхней 23 и нижней обвязок, а также вертикальных элементов 22 замкнутого поперечного сечения, сваренных из Ω- и Z-образных профилей. В закрытом положении дверь удерживается запорами — нижним 19 и верхним, состоящим из клина 24 и направляющих с упорами 25 для клина, приваренных соответственно к правой и левой створкам двери. В открытом положении двери располагаются вдоль боковых стен и удерживаются специальными поворачивающимися скобами 28, вставляемыми в отверстия 29 на верхних обвязках кузова. По концам кузов оборудован наружными 1 и внутренними лестницами, а также подножками 2 и поручнями, предназначенными для обслуживающего персонала.
www.vagoni-jd.ru
Конструкция специализированного полувагона — МегаЛекции
Повышение технического уровня вагонного парка железных дорог России и стран СНГ достигается в настоящее время за счет увеличения доли специализированных полувагонов повышенной грузоподъемности с глухим кузовом, т.е. без разгрузочных люков в полу и с торцевыми жесткими стенами. Используя современные механизированные средства и методы производства погрузочно-разгрузочных операций, а также гравитационные свойства сыпучих грузов, специализированные полувагоны с глухим кузовом обеспечивают в эксплуатации значительный технико-экономический и социальный эффект.
Специализированный четырехосный полувагон модели 12-1592 грузоподъемностью 71 т имеет цельнометаллический сварной кузов, боковые стенки которого состоят из каркаса и обшивки из гнутого листа с периодическими гофрами. Торцевые стены состоят из верхней обвязки гнутого профиля, двух боковых швеллеров № 14, двух горизонтальных поясов жесткости омегообразного профиля 110 х 135 х 55 х 6 из гладкой листовой стали толщиной 5 мм.
Специализированный четырехосный полувагон модели 12-1505 (рис.2) разработан на базе универсального полувагона, у которого разгрузочные люки в полу заменены сплошным металлическим настилом 1, а торцевых дверей нет.
Для стока воды и зачистки кузова при подготовке полувагона под погрузку в полу предусмотрены два люка 2, расположенные по диагонали и открывающиеся внутрь кузова. Рама 3 кузова 4 вагона отличается от рамы универсального полувагона тем, что в ней для поддержания металлического настила пола между хребтовой балкой и нижними обвязками боковых стен кузова установлено по дополнительной продольной балке из двутавра № 18. Остальные элементы кузова мало отличаются от элементов кузова универсального полувагона.
Рисунок 2- Специализированный четырехосный полувагон модели 12-1505
Более современную конструкцию кузова и лучшие технические характеристики имеет специализированный четырехосный полувагон модели 12-580грузоподъемностью 71т с глухим кузовом. Внутренняя высота кузова объемом до 83 м³ увеличена за счет отсутствия двутавра на хребтовой балке.
Специализированный четырехосный полувагон модели 12-4004 (рис.3) для перевозки технологической щепы от мест ее производства к предприятиям целлюлозно-бумажной промышленности по магистральным железным дорогам и по путям промышленного транспорта имеет цельнометаллический сварной кузов.
Рисунок 3- Специализированный четырехосный полувагон модели 12-4004
Боковая стена кузова состоит из каркаса, обшитого металлическими листами двух типов толщиной 3 и 4 мм из гнутых профилей с периодически повторяющимися гофрами. Верхняя составная обвязка замкнутого поперечного сечения сделана из гнутого профиля и уголка. Нижняя обвязка изготовлена из прокатного уголка сечением 160 х 100 х 10 мм. Рама кузова состоит из хребтовой балки, из двух зетов № 31 и двутавра № 19; шкворневых балок коробчатого поперечного сечения из листов толщиной 10 мм; двух концевых балок коробчатого поперечного сечения из двух швеллеров № 27. Верхняя обвязка торцевых стен изготовлена из замкнутого прямоугольного профиля сечением 60 х 80 х 8 мм, а нижняя обвязка — из гнутого уголка сечением 180 х 100 х 8 мм. Поперечные пояса торцевой стены кузова изготовлены из специального профиля, а боковые стойки стены — из швеллера № 12. Обшивка торцевой стены из гладких листов толщиной 5 мм. В полу кузова 22 разгрузочных люка, закрываемые унифицированными крышками.
На Уралвагонзаводе разработаны и построены образцы большегрузных специализированных восьмиосных полувагонов с глухим кузовом габарита 1-Т грузоподъемностью 131 т (модель 12-538) и габарита Т грузоподъемностью 132 т (модель 12-538), в котором впервые в вагоностроении применена более совершенная и надежная шпангоутная заделка боковых стен кузова в раму полувагона. Кузова этих полувагонов изготовлены с наклонными внутрь вагона стенами для облегчения выгрузки сыпучих грузов. Для перевозки крупнокусковой медной руды от мест ее добычи до металлургических предприятий применяются восьмиосные специализированные полувагоны модели 22-4024 грузоподъемностью 115 т. Погрузка руды в полувагоны производится экскаваторами с ковшами объемом 6-8 м³, а выгрузка — с помощью вагоноопрокидывателей. Цельнометаллический сварной кузов полувагона изготовлен как одна целая конструкция. Рама кузова состоит из двух усиленных зетов № 31 (у), двух концевых, двух шкворневых балок из прокатных металлических листов толщиной 10, 12, 14 мм и промежуточных поперечных балок из гнутого профиля 200 х 120 х 10 мм. Настил пола сделан из стальных листов толщиной 10 мм, каркас боковой стены кузова — из стоек гнутого профиля сечением 160 х 80 х 7 мм, нижняя обвязка — из специального гнутого профиля. Каркас торцевой стены состоит из двух угловых стоек из уголка 125 х 125 х 10, двух вертикальных стоек корытообразного профиля с толщиной стенок 8 мм, верхней обвязки замкнутого профиля 160 х 80 х 7 м и концевой балки рамы полувагона, являющейся также нижней обвязкой. Каркас кузова внутри покрыт обшивкой из металлических листов толщиной 10 мм.
Специализированный полувагон-хоппер модели 22–471(рис.4) предназначен для перевозки горячих окатышей и агломерата с температурой груза до 700°С с места производства на приемные бункера доменной печи. Его характеристика: грузоподъемность 65 т, тара 23 т, объем кузова 42 м3, длина по концевым балкам рамы 10,78 м, габарит 1-ВМ.
Рисунок 4- Специализированный полувагон-хоппер модели 22–471
Кузов полувагона-хоппера имеет раму 4, две боковые 2 вертикальные, две торцовые 1 стены с углом наклона 41° к плоскости рамы и два бункера с двумя разгрузочными люками 3 размером 3500х400х560 мм. Рама кузова состоит из хребтовой балки, двух концевых, шкворневых и поперечных балок.
Хребтовая балка выполнена из двух двутавров № 45, перекрытых сверху и снизу листами. Концевые, шкворневые и поперечные балки сварные соответственно корытообразного, коробчатого и двутаврового сечений. Каркас боковой стены изготовлен из прокатных и гнутых профилей: верхний пояс коробчатого сечения из швеллера № 14 и гнутого элемента, нижний пояс и шкворневая стойка – из замкнутого прямоугольного профиля коробчатого сечения размером 160х80х7 мм. Нижний и верхний пояса соединены между собой двенадцатью стойками. Промежуточные стойки выполнены из швеллера № 14. Каркас торцовой стены сварен из швеллеров № 10 и 14. Обшивка стен представляет собой набор панелей из гнутого профиля, которые не имеют жесткого соединения с каркасом, что обеспечивает их подвижность при температурных расширениях для предупреждения коробления несущих элементов кузова.
Крышки разгрузочных люков бункеров открываются и закрываются при помощи специального механизма разгрузки, который расположен под бункерами и представляет собой систему рычагов, приводимых в действие от пневматических цилиндров с дистанционным управлением. Крышка люка представляет собой каркас рамной конструкции, обшитый гофрированными листами. К нижнему поясу приваривается козырек, который в закрытом положении находится под нижней обвязкой кузова, создавая тем самым надежное уплотнение от просыпания окатышей. С торцов крышки уплотнение создается за счет выступающих листов, которые в закрытом положении помещаются в пазах люков. Механизм разгрузки имеет систему рычагов 2,5,6, связывающих крышки люков 1 с валом 7, который посредством шестеренчатой пары 3 под действием двух пневматических цилиндров 4 поворачивается на определенный угол, открывая или закрывая при этом крышки разгрузочных люков. Закрытие крышек происходит благодаря переходу соединяющих их рычагов через «мертвую точку».
Заключение
Современный этап развития отечественного вагоностроения характеризуется дальнейшим совершенствованием конструкций крытых вагонов и полувагонов. В частности появились полувагоны моделей 12-196 и 12-197 с новой конструкцией торцевых и боковых стен, вагон-хоппер модели 19-569 с рамой без хребтовой балки и овальным поперечным сечением кузова и целый ряд других вагонов нового поколения.
Основными побудительными причинами постоянного прогрессирующего развития конструкций вагонов являются:
· изменение условий эксплуатации (объема и состава грузооборота) и, соответственно, рациональных значений технико-экономических параметров вагонов;
· появление новых конструкционных материалов;
· совершенствование технологии изготовления;
· стремление к повышению надежности конструкций путем устранения недостатков вагонов предыдущего поколения;
· постоянное совершенствование ходовых частей, автосцепного и тормозного оборудования.
Список литературы
1) «Конструкция вагонов» И.Ф.Пастухов, В.В.Пигунов, Р.О.Кошкалда
2) «Конструирование и расчет вагонов» В.В.Лукин, П.С.Анисимов, В.Н.Котуранов, 2011г.
3) http://myrailway.ru/directory/specializirovannye-gruzovye-vagony
4) http://ga-avto.ru/tramvaj/14.html
Рекомендуемые страницы:
Воспользуйтесь поиском по сайту:
megalektsii.ru
1.3 Общие сведения об устройстве вагонов
Все вагоны состоят из следующих основных узлов; кузова с рамой, ходовых частей, автосцепных устройств и тормозного оборудования.
Кузов служит для размещения в вагоне пассажиров или грузов. Конструкция кузова зависит от назначения загона. Так, каркас кузова грузовых крытых вагонов состоит из металлических стоек, дуг и балок фасонного профиля. Стены кузова обшиты стальными листами. Если стены обшиваются досками, то каркас кузова дополнительно имеет металлические раскосы. Потолочные дуги и фрамуги покрыты стальными листами, сваренными в стыках и образующими цельнометаллическую крышу. Раньше крыша грузового вагона покрывалась кровельной сталью, делалась без загрузочных люков и была менее прочной и недолговечной. Кузов имеет по две (или по одной) задвижной цельнометаллической двери с обеих сторон и по два люка на каждой продольной стене.
Каркас кузова цельнометаллического пассажирского вагона представляет единую сварную металлическую несущую конструкцию, состоящую из поперечных и продольных балок и стоек, а также дуг крыши. Наружная обшивка и крыша выполнены из стальных гофрированных листов, привариваемых к каркасу. Такой кузов обладает большой прочностью и меньшей массой, приходящейся на одно пассажирское место. Внутренние перегородки, а также внутренняя обшивка стен выполнены из дерева, древесноволокнистых плит и полимерных материалов.
Основание кузова — рама воспринимает продольные ударно-тяговые силы, действующие на вагон, и массу груза. Хребтовая балка рамы современных грузовых вагонов состоит из двух мощных стальных прокатных швеллерных или 2-образных балок, расположенных одна от другой на расстоянии, обеспечивающем размещение устройств автосцепки. Обе балки скреплены между собой стальными листами и образуют единую мощную конструкцию. К хребтовой балке прикреплены концевые (буферные) балки, поперечные и шкворневые балки, скрепленные боковыми продольными балками. Конструкция рамы полувагона или цистерны позволяет закрепить разгрузочные люки или котел.
Кузов опирается на ходовые части, которые передают на рельсы массу вагона с грузом.
К ходовым частям вагона относятся колесные пары, буксы с подшипниками, рессорное подвешивание. В четырехосных и многоосных вагонах все эти элементы объединяются в тележки, которые и обеспечивают более легкое прохождение вагонов на кривых участках пути и более плавный ход.
Основной тип тележки грузовых вагонов — двухосная тележка ЦНИИ-ХЗ с одинарным рессорным подвешиванием. Она состоит из двух литых боковин, в которых имеется средний проем (окно) для размещения пружин рессорных комплектов. В пазы боковых проемов вставлены корпуса букс колесных пар. Литая надрессорная балка тележки представляет собой брус коробчатого сечения, воспринимающий нагрузку от вагона через пятниковое соединение. Концы балки опираются на клиновые амортизаторы и через них на комплекты пружин. Клинья амортизаторов размещены в особых углублениях и соприкасаются своими вертикальными плоскостями со стальными сменными планками, укрепленными на боковинах. В зависимости от массы груза вагона каждый рессорный комплект тележки состоит из пяти — семи двухрядных пружин. Колесные пары для этой тележки имеют диаметр по кругу катания 950 мм.
На кронштейнах боковин валиками укреплены подвески триангелей с тормозными колодками. Триангели соединены с вертикальными рычагами, а последние — с распорной тягой при помощи валиков, шайб и шплинтов.
Для шестиосных грузовых вагонов построены трехосные тележки. а для восьмиосных — четырехосные, состоящие из двух сочлененных двухосных тележек типа ЦНИИ-ХЗ.
Под грузовыми вагонами еще имеется некоторое количество двухосных тележек с боковинами, отлитыми заодно с буксами, и поясные тележки, которые постепенно заменяются тележками типа ЦНИИ-ХЗ.
Тележка двухосная КВЗ-ЦНИИ — наиболее совершенный тип тележки пассажирского вагона. Сварная рама тележки опирается на надбуксовые цилиндрические рессоры и через них на опоры роликовых букс колесных пар. Тележка имеет центральное рессорное подвешивание, состоящее из четырех трехрядных пружин, двух люлечных балок, четырех люлечных подвесок и боковых гидравлических гасителей колебаний. Тележки для вагонов массой брутто до 70 т имеют по одному с каждой стороны гидравлическому гасителю колебаний, а для вагонов массой брутто выше 70 т — по два гасителя.
Тележка цельнометаллических пассажирских вагонов прежних выпусков имеет центральное люлечное подвешивание, снабженное эллиптическими рессорами без гидравлических гасителей колебаний.
Вагоны с такими тележками могут быть использованы для скоростей движения до 120 км/ч.
К основным характеристикам грузовых вагонов относятся:
Грузоподъемность — максимальная масса груза в тоннах, которую можно перевозить в вагоне данного типа; длина вагона; тара — масса порожнего вагона; коэффициент тары — отношение массы порожнего вагона к грузоподъемности. Чем ниже коэффициент тары, тем экономичнее вагоны.
Допустимые нагрузки от оси вагона на рельсы (осевая), а также от вагона на 1 м пути определяют максимально возможную массу загруженного вагона (брутто).
Объем кузова и площадь пола определяют вместимость вагона. У открытого подвижного состава (платформ, полувагонов) важное значение имеет высота бортов или стен. При проектировании вагонов учитывается соотношение вместимости кузова и грузоподъемности. Вместимость крытого вагона характеризуется удельным объемом кузова, или отношением объема кузова вагона к его грузоподъемности, а вместимость платформы — удельной
площадью пола, или отношением площади пола к грузоподъемности.
Для пассажирских вагонов основной конструкционной характеристикой является отношение тары к числу мест для пассажиров.
Чем меньше масса тары, приходящейся на каждое место, тем экономичнее вагон.
studfiles.net
Технология ремонта кузова полувагона | Курсовые проекты
Страница 1 из 5
Железнодорожный транспорт является основным видом транспорта России, имеет важнейшие значение для нашей страны. Большое значение имеет рациональность конструкции вагонов и их технико-экономических показателей, провозную способность дорог, возможность широкого внедрения механизации и автоматизации при изготовлении и ремонте вагонов, а также их эксплуатации. Большую часть парка железнодорожных вагонов составляют грузовые вагоны различных типов.
Полувагоны составляют значительную часть грузового вагонного парка, используемую наиболее интенсивно. Полувагон не имеет крыши, а пол его составлен из разгрузочных люков.
НАЗНАЧЕНИЕ ПОЛУВАГОНОВ
Полувагоны предназначены для перевозки массовых сыпучих и навалочных грузов, не требующих защиты от атмосферных осадков,— руды, леса, угля, металла, а также автомашин, сельскохозяйственной техники и др. Этот тип вагона позволяет широко применять механизированную погрузку и выгрузку, в том числе и на вагоноопрокидывателях. Перевозка таких массовых грузов, как руда, каменный уголь, лес и др., осуществляется маршрутами. Практика показала, что для маршрутных перевозок массовых тяжелых грузов, особенно на грузонапряженных направлениях, нужны большегрузные восьмиосные полувагоны с повышенными нагрузками на 1 м пути.
Универсальные четырёхосные полувагоны модели 12-753 спроектированы по габариту 0-ВМ и предназначены для перевозки сыпучих, крупнокусковых, штучных и других грузов, не требующих защиты от атмосферных осадков. Кузова этих полувагонов цельнометаллические, выполнены из типовых профилей.
Полувагоны оборудованы подножками и поручнями, необходимыми для безопасной работы составителей, а также наружными и внутренними лестницами, расположенными по диагонали на боковых стенах с внутренней и наружной сторон кузова. Для навески поездных сигналов кузова снабжены кронштейнами, а для увязки и крепления груза снаружи и внутри кузова оборудованы скобами и кольцами. Для возможности перевозки лесоматериалов с «шапкой» предусмотрены скобы для установки лесных стоек. Для подтягивания вагона с помощью лебёдки снаружи кузова приварены чалочные приспособления.
НЕИСПРАВНОСТИ КУЗОВА ПОЛУВАГОНА И ПРИЧИНЫ ИХ ВОЗНИКНОВЕНИЯ
Наиболее характерными неисправностями кузова являются трещины, пробоины, прогибы, вмятины, коррозионные повреждения металлических деталей. Основными причинами возникновения неисправностей являются нарушение правил погрузки и выгрузки грузов, правил маневровых работ и нарушение тех. процесса ремонта.
ДЕФЕКТАЦИЯ И РЕМОНТ КУЗОВА ПОЛУВАГОНОВ
Кузов
Кузов полувагона цельнометаллический, с четырнадцатью разгрузочными люками в полу и двустворчатыми торцевыми дверями. Он состоит из рамы, двух боковых и двух торцевых стен, а также пола, образованного крышками люков. Торцевые створки двери навешиваются тремя петлями на кронштейны угловых стоек боковых стен и при необходимости открываются вовнутрь. Левая створка фиксируется в закрытом положении нижним запором в виде закидки, а правая – верхним клиновым запором. Наружная лестница и поручень установлены для удобства обслуживания вагона в эксплуатации.
Рисунок – Элементы кузова полувагона
Для придания необходимой прочности крепления угловых стоек к концевым балкам рамы и нижним обвязкам стен их соединения усилены накладками. Соединения промежуточных стоек с поперечными балками рамы также усилены накладками. На концевых балках рамы предусмотрены посадочные места для постановки буферных стаканов на случай сцепления с вагонами, оборудованных винтовой стяжкой.
Ремонт элементов кузова полувагона сваркой, производится в соответствии с действующей ремонтной документацией на производство сварочных и наплавочных работ при ремонте грузовых вагонов.
Прогибы верхней обвязки без усиления накладками устраняют правкой. Допускается оставлять без ремонта прогиб верхней обвязки не более 10 мм на 1 м длины между стойками.
Трещину или излом верхней обвязки допускается устранять сваркой с последующей постановкой накладки или вставками. После ремонта, при замене частей верхней обвязки, допускается не более одного стыка между смежными стойками, но не более 3-х на одной стене полувагона.
Допускается оставлять без ремонта местные вмятины, не имеющие трещин на стойках кузова омегообразного профиля глубиной не более 30 мм. При глубине, более указанной, разрешается ставить декоративные накладки.
При одновременном вертикальном изгибе верхней и нижней обвязок (стенок) кузова сверх установленных допусков, (более 10 мм на 1 м длины или более 25 мм на всю длину стены) металлическую обшивку по стойкам на высоту прогиба срезают, выправляют обвязки и устанавливают новую вставку металлической обшивки с последующей ее приваркой катетом сварочного шва 5 мм. Допускается полная замена верхней обвязки.
Рисунок 3.1.2 – Установка вставки металлической обшивки
Рисунок 3.1.3 – Ремонт верхней обвязки (вариант ремонта замены обвязки)
Вмятины на металлической обшивке глубиной более 40 мм выправляют, трещины заваривают с постановкой накладки с внутренней стороны. Листы с коррозией более половины площади листа с глубиной более 0,5 толщины листа заменяют новыми. Нижнюю обвязку полувагона, имеющую коррозионные повреждения более 1/3 толщины элемента на длине 1/3 длины ремонтируют сваркой с последующим усилением поврежденных мест односторонними накладками, перекрывающими поврежденные места не менее 50 мм на сторону. При коррозионных повреждениях более 1/3 толщины на длине более 1/3 длины нижнюю обвязку заменяют.
При ремонте нижней обвязки в месте установки и приварки накладки разрешается вырезать часть нижней кромки металлической обшивки на длину устанавливаемой накладки.
Трещины нижней обвязки заваривают, зачищают до основного металла, устанавливают накладку с последующей обваркой сплошным швом по всему периметру. Допускается перекрывать трещины одной накладкой, если расстояние между ними менее 150 мм. Накладка должна дополнительно крепиться электрозаклепками в количестве не менее двух.
Вырывы на горизонтальной полке допускается ремонтировать вставкой в количестве не более двух штук с установкой накладки и обваркой сплошным швом. Поперечные швы не допускаются.
При наличии на штампованной стойке омегообразного сечения одного из дефектов: излома, трещины, выходящей на вертикальные стенки, коррозии более 1/3 толщины или подреза полок стойки более 20 мм и расположении поврежденного места на расстоянии менее 300 мм от верхней кромки, нижней обвязки кузова, разрешается ремонтировать стойку на месте, путем постановки новой части стойки на высоту не менее 300 мм от верхней кромки нижней обвязки. При этом стойку соединяют с новой частью односторонним сварным швом с приваркой усиливающей накладки толщиной 6 мм, перекрывающий сварной шов не менее 50 мм на сторону с последующей обваркой накладки по всему периметру. Нижнюю часть стойки, приваренную к нижней обвязки дополнительно крепят электрозаклепками диаметром 20 ±1 мм.
1 – нижний обвязочный угольник; 2 – стойка кузова; 3 – электрозаклепка
Рисунок 3.1.4 – Дополнительное крепление стойки электрозаклепками
Допускается производить замену стойки. При коррозии менее 1/3 толщины полок их ремонтируют постановкой усиливающей накладки. При подрезе полок сваркой до10 мм разделывают швы с последующей приваркой стоек. При подрезе полок сваркой более 10 мм, но не более 20 мм, сварочные швы разделывают, стойки приваривают с последующей приваркой усиливающих накладок с той и другой стороны стойки.
Рисунок 3.1.5 – Варианты ремонта стоек кузова
Накладка должна перекрывать расстояние от краев подреза не менее 30 мм с плавным переходом к краю полке. Ремонтировать таким способом две рядом стоящие стойки на вагоне — запрещается.
Если трещина на стойке гнутого профиля не переходит на вертикальную стенку, трещину разрешается заваривать с последующей постановкой усиливающей накладки. Таким образом, разрешается устранять трещины на обеих горизонтальных полках стойки.
При установке новой стойки кузова, её приваривают односторонним сварным швом к верхней обвязке. При этом усиление верхней обвязки снимают с последующим его восстановлением.
Трещины в металлической обшивке длиной до 100 мм заваривают без постановки усиливающей накладки. Местные прожоги листа металлической обшивки устраняют сваркой. Все трещины длиной более 100 мм заваривают с последующей постановкой усиливающей накладки толщиной 4 мм с внутренней стороны кузова с обваркой ее по периметру. При этом усиливающая накладка должна перекрывать трещину не менее 30 мм с каждой стороны. В одном пролете разрешается заваривать не более двух таких трещин с расстоянием между ними не менее 1000 мм. Таким способом устраняют продольные прожоги, образовавшиеся на металлической обшивке при срезке элементов боковой стены.
Допускается использовать для нескольких трещин одну накладку, площадь которой не должна превышать 0,3 м2.
При пробоине в металлической обшивке на выправленные кромки устанавливают усиливающую накладку толщиной 4 мм с обваркой с наружной стороны сплошным швом, а с внутренней стороны прерывистым сварным швом.
Лучевые трещины от пробоины не допускается, при ремонте обшивки их следует вырезать и установить накладку с внутренней стороны, перекрывающую дефектное место не менее чем на 30 мм, обваривать по периметру сплошным швом. Коррозионные повреждения металлической обшивки допускается не более 1 мм толщины листа (или профиля). При повреждении более 1 мм толщины металла обшивку ремонтируют постановкой накладок толщиной 4 мм, перекрывающих дефектное место не менее чем на 30 мм на сторону. Накладки должны соответствовать профилю обшивки и привариваться снаружи по всему периметру с катетом шва 4 мм.
Разрешается смена одной части обшивки (по верхнему или нижнему краю) шириной до 400 мм на всю длину между смежными стойками или по ГОСТ 5264-80.
При коррозионном повреждении более 1 мм толщины листа и более 50% площади листа между смежными стойками лист полностью заменяют с приваркой его к верхней и нижней обвязкам и к стойкам.
Допускается:
- при наличии двух и более трещин, суммарная длина которых превышает 500 мм, которые нельзя перекрывать одной усиливающей накладкой площадью 0,3 м2.
- при наличии пробоин, суммарная площадь которых более 0,3 м2;
- при необходимости одновременной смены по верхнему и нижнему краям.
На угловых стойках допускается ремонтировать не более одной трещины длиной до 100 мм без установки усиливающих накладок и до 0,5 поперечного сечения стойки с постановкой усиливающей накладки.
Суммарное уширение или сужение боковых стен в средней части полувагона должно быть не более 30 мм от предельных размеров, а одной боковой стены не более 15 мм. Уширение боковых стен в плоскости дверей более 10 мм от предельных размеров не допускается.
3.2 Крышки люков полувагонов
Крышки люков снимают для осмотра, ремонта и замены, а также для замены типовыми не менее десяти крышек. На полувагонах с невыработанным сроком службы, заменяют крышки люков, имеющие толщину сечения листа менее 4 мм на площади более половины листа.
Толщину замеряют между гофрами при расстоянии от 450 до 500 мм от козырька или передней отбортовки. Крышки люков должны изготавливаться из стали 09Г2Д или стали 10ХНДП ГОСТ 19281 и отвечать действующим «Нормам для расчета и проектирования вагонов железных дорог МПС колеи 1520 мм (несамоходных)», ГосНИИВ-ВНИИЖТ 1996 г.
Петли крышек люков заменяют типовыми в случае износа отверстий под валик более 2 мм или изломов. Крышки люков с трещинами или с местными выработками ремонтируют в соответствии с действующей ремонтно-технической документацией на производство сварочных работ. Новые крышки люков полувагонов, должны быть изготовлены по чертежам, согласованным с Департаментом вагонного хозяйства. Крышки люков должны легко открываться и закрываться. Запрещается устанавливать нетиповые валики.
Крышки люка, имеющие приклёпанные кронштейны, должны быть заменены на новые литые с косо расположенными кронштейнами.
Торсионы осматривают, неисправности в них устраняют, с трещинами, изломами заменяют новыми, трущиеся поверхности смазывают.
Механизмы для облегчения подъема крышек люков торсионно-рычажного типа разбирают, детали осматривают, поврежденные ремонтируют или заменяют новыми, отсутствующие заменяют.
Суммарный износ в шарнирных соединениях рычагов не должен превышать 2 мм. При износах более 2 мм заменяют на новые.
Угол закручивания торсиона определяют по его положению в разъединенном состоянии и измеряют от вертикальной оси. При этом наклон нижнего рычага от вертикальной оси должен составлять от 25° до 35°.
Место установки кронштейна у хребтовой балки тщательно осматривают. При наличии трещин по сварке швы разделывают до основного металла и заваривают. При выработке металла хребтовой балки на месте установки ушка разрешается приваривать по всему периметру вставку толщиной 10,5 мм из стали 09Г2 ГОСТ 19281с Х-образной разделкой кромок и зачисткой сварного шва заподлицо с основным металлом.
Все соединения торсионно-рычажного механизма смазывают смазкой УСсА ГОСТ 3333. Допускается применять отработанную смазку ЛЗ-ЦНИИ. При собранном торсионно-рычажном механизме, крышка люка должна подниматься усилием одного человека.
В открытом состоянии крышки люков у четырехосных полувагонов должны ложиться на оба упора, для чего разрешается наращивать один из упоров приваркой прокладки или наплавлять поверхности упора с последующей механической обработкой на величину до полного прилегания крышки люка.
1 – опора; 2 – торсион; 3 – рычаг; 4 – валик; 5 – шайба; 6 – шплинт; 7 — ушко
Рисунок 3.2.1 – Механизм подъема крышек люков
НачалоПредыдущая 1 2 3 4 5 Следующая > Последняя >>
texttotext.ru
Лабораторная работа № 2 общее устройство грузовых вагонов
Цель работы: ознакомиться с общим устройством грузовых вагонов.
Общие сведения
Парк грузовых вагонов состоит из универсальных (перевозят грузы широкой номенклатуры) и специализированных (перевозят один вид груза или несколько однородных) вагонов пяти основных видов: крытые вагоны, платформы, полувагоны, изотермические.
К специализированным вагонам относятся живорыбные, вагоны для технических и бытовых нужд железных дорог (вагоны-мастерские, вагоны восстановительных и пожарных поездов) и др. Конструкция кузова грузового вагона и его оборудование должны обеспечивать сохранность груза, наибольшую вместимость, высокую производительность труда и удобство работы при погрузке и выгрузке.
По условиям эксплуатации грузовые вагоны разделяются на общесетевые, которые допускаются к эксплуатации по железным дорогам нашей страны, и вагоны промышленного транспорта, которые могут перемещаться в груженом состоянии только по внутризаводским и другим промышленным путям замкнутого направления.
Тип грузового вагона и общее устройство определяются его назначением и конструкцией кузова, в котором основанием и наиболее нагруженной частью является рама (бывают кузова безрамные).
В зависимости от рода перевозимых грузов кузова разделяются на открытые (у платформ, полувагонов, думпкаров, хопперов и др.) и закрытые (у крытых вагонов, цистерн, изотермических, зерновозов, цементовозов и др.). Кузова могут быть цельнометаллическими или с металлическим каркасом и деревянной обшивкой, а по технологии изготовления сварными или клепанными.
Открытые кузова платформ и полувагонов используются для перевозки металлических и деревянных контейнеров и грузоподъемностью 2,5 т; 5 т; 10 т; 20 т и 30 т с размещенными в них штучными и другими грузами. Для исключения перегрузок из вагонов в автомобили применяют контрейлеры – специальные контейнеры, приспособленные для подкатки автомобильных шасси
Вагон любого типа должен обеспечивать требуемую прочность при минимальном весе, быть надежным в течение всего срока службы, дешевым при изготовлении и при ремонте, удобным и нетрудоемким в эксплуатации.
Крытые вагоны
Универсальный 4-осный крытый вагон модели 11-217
Рис. 3.
Предназначены для перевозки разнообразных грузов и обеспечения их сохранности и защиты от атмосферных воздействий. При оснащении соответствующим оборудованием, могут быть использованы и для массовых перевозок людей. В боковых стенах кузова универсального крытого вагона (рис. 3) имеются задвижные двери и по два люка с металлическими крышками. Они служат для освещения, вентиляции и загрузки сыпучими грузами. Люки могут быть и в крыше. С 1974 г. выпускаются 4-осные вагоны с грузоподъемностью до 68 т.
Специализированные крытые вагоны весьма разнообразны.
Кузов специализированного вагона (рис. 4) цельнометаллический двухъярусный. Рама образует нижний ярус кузова. Имеются торцевые двери, и переездные площадки для свободного проезда автомобилей по всему составу в средней части вдоль боковых стен есть проемы, закрытые металлической сеткой.
Таблица 5
Технические характеристики крытых вагонов
Крыша специализированного вагона (рис. 5) металлическая с термоизоляцией 50 мм. На боковых стенах размещены задвижные двери облегченного типа. Внутри вагона на каждом ярусе вдоль одной из боковых стен установлены кормушки и поилки для скота. В кузове размещается трехсуточный запас кормов.
Двухъярусный крытый вагон для легковых автомобилей модели 11-835
Рис. 4.
Планировка крытого вагона для перевозки скота модели 11-240
Рис. 5.
Кузов специализированного саморазгружающегося вагона (рис. 6) образует крыша, боковые стены, наклонные торцевые стены и рама. Имеется шесть бункеров (по три с каждой стороны) с механизмами для открытия и закрытия люков, на которых могут быть установлены вибраторы, облегчающие разгрузку. В крыше имеются четыре загрузочных люка.
Крытый вагон-хоппер для зерна модели 19-752
Рис. 6.
Платформы
Платформы предназначены для перевозки длинномерных и тяжеловесных грузов. Универсальные платформы (рис. 7) строят с боковыми и торцевыми откидными бортами, шарнирно связанными с рамой. Имеются приспособления для установки стоек при перевозке бревен, столбов, досок и т.п. Грузоподъёмность 4-осных платформ постройки 1974 г. до 70 т.
Универсальная 4-осная платформа модели 13-4012
Рис. 7
Специализированные 4-осные платформы перевозят болшегрузные контейнеры, легковые автомобили и др. К специальному виду подвижного состава относятся 416-осные транспортеры платформенного типа грузоподъемностью 55220 т для перевозки тяжеловесных, крупногабаритных грузов, которые не размещаются на других типах платформ. Это трансформаторы, роторы крупных электрогенераторов, большие станки, прессы, части гидротурбин и др.
Специализированная платформа (рис. 8) перевозит шесть контейнеров массой брутто 10 т, или три контейнера массой брутто 20 т, или один контейнер массой брутто 30 т и один массой брутто 20 т. Для крепления контейнеров имеется десять поворотных и четыре неподвижных упора.
Платформа перевозки большегрузных контейнеров модели 13-470
Рис. 8
Специализированная платформа (рис. 9) строилась в период 1970-1982 гг. На платформе размещаются 17 автомобилей «Жигули»или «Запорожец», 10 — «Москвич» или 8 — «Волга». Кузов платформы состоит из нижней и верхней рам с металлическим настилом пола, четырех концевых и двух средних стоек. Автомобили на платформе крепятся с помощью 68 колесных упоров, постоянно укрепленных на вагоне. Для подъема на верхнюю раму платформа оборудована лестницами.
Двухъярусная платформа для легковых автомобилей модели 13-479
Рис. 9
Таблица 6
Технические характеристики платформ
Кузов транспортера (рис. 10) имеет пониженную погрузочную площадку благодаря изогнутой форме главной балки. Тележки транспортера объединены специальными концевыми балками. Грузоподъемность составляет 150 т. Крепление груза осуществляется через специальные отверстия в верхнем листе погрузочной площадки.
12-осный транспортер платформенного типа
Рис. 10
Полувагоны
Предназначены для перевозки массовых навалочных, сыпучих грузов (каменный уголь, руда, кокс, щебень, гравий и др.) и является наиболее распространенным типом вагонов грузового парка.
Кузов универсального полувагона (рис. 11) выполнен без крыши, имеются открывающиеся внутрь торцевые двери и разгрузочные люки в полу вдоль боковых стен. Сыпучие грузы через люки разгружаются по обе стороны вагона без использования дополнительных устройств. Торцевые двери необходимы для загрузки длинномерных грузов и самоходной техники.
Универсальный 8-осный полувагон с торцевыми дверьми модель 12-541
Рис. 11
Кузова некоторых универсальных полувагонов могут быть построены с глухими торцевыми стенами (рис. 12), приваренными к боковым стенам. Разгрузка производится через люки, объем кузова увеличен благодаря глухим торцевым стенам.
Универсальный 4-осный полувагон с глухими торцевыми стенами
модель 12-119
Рис. 12
Специализированный полувагон-хоппер модель 22-471
Рис. 13
Специализированные полувагоны строят с глухим кузовом, т.е. без торцевых дверей и люков в полу. Они предназначены для перевозки сыпучих грузов в замкнутых маршрутах с разгрузкой на вагоноопрокидывателях.
Таблица 7
Технические характеристики полувагонов
Разновидностью специализированных полувагонов являются 4-осные вагоны-хопперы (рис. 13) для перевозки сыпучих и пылевидных грузов грузоподъемностью до 64-67 т. Вагон-хоппер имеет высокие боковые стены, а в случае перевозки цемента еще и крышу. Торцевые стены наклонены к середине вагона, где расположены разгрузочные люки. Вагоны-хопперы используют в основном на закрытых маршрутах и для хозяйственных нужд.
Цистерны
Цистерны предназначены для перевозки жидких, газообразных, затвердевающих и порошкообразных грузов.В зависимости от рода перевозимых грузов цистерны разделяются на цистерны общего назначения или универсальные — служат для перевозки нефтепродуктов широкой номенклатуры, и специализированные — для перевозки отдельных видов грузов. Цистерны общего назначения (рис. 14) в свою очередь подразделяются на цистерны для перевозки светлых (бензин, керосин, лигроин и др.) и вязких (нефть, минеральные масла и др.) нефтепродуктов.Специализированные цистерны подразделяются на цистерны для перевозки высоковязких грузов, пищевых продуктов, кислот, сжиженных газов, порошкообразных, затвердевающих и некоторых других грузов.
4-осная цистерна общего назначения модель 15-1443
Рис. 14
Кузов цистерны (котел) представляет собой металлический сварной резервуар цилиндрической формы с двумя днищами, люками в верхней части для налива груза, очистки и ремонта котла, а также с универсальными сливными приборами в нижней части. Внутренняя поверхность цистерн для перевозки агрессивных жидкостей (кислоты, сера, сжиженные газы и др.) покрываются защитным слоем (эмаль, свинец, резина и др.). Котел изготавливают из нержавеющей стали, алюминиевых сплавов. Цистерна для перевозки молока имеет снаружи термоизоляционное покрытие.
Специализированные цистерны во многом сходны с универсальными и отличаются главным образом наличием устройств и средств для защиты от воздействия солнечной радиации (перевозка хлора, аммиака), для разогрева груза перед сливом (перевозка серы, фосфора) и др.
Специализированная цистерна для перевозки молока (рис. 15) имеет котел, разделенный двумя перегородками на три секции для перевозки молока различного качества. Сверху имеются три люка для налива, а внизу устройство слива. Толщина слоя термоизоляции 300 мм.
Цистерна для перевозки молока модель 15-886
Рис. 15
Снаружи котлы всех цистерн имеют лестницы с поручнями.
Таблица 8
Технические характеристики цистерн
Изотермические вагоны
Изотермические вагоны служат для перевозки скоропортящихся грузов (СПГ): мяса, рыбы, масла, фруктов, овощей и т. д. По назначению изотермические вагоны делятся на универсальные и специализированные. Универсальные вагоны предназначены для перевозки всех видов скоропортящихся грузов. К ним относятся все рефрижераторные вагоны и вагоны-ледники. Специализированные вагоны приспособлены для перевозки отдельных грузов, например молока, живой рыбы, вина. По способу охлаждения и способу отопления вагоны делятся на вагоны с машинным охлаждением и электрическим отоплением (рефрижераторные) и охлаждаемые водным льдом или льдосоляной смесью, а отапливаемые печами-времянками (вагоны-ледники). Рефрижераторные вагоны выпускаются в индивидуальном (автономном) и секционном исполнении.
Грузовой вагон 5-вагонной рефрижераторной секции типа РС-4 БМЗ
Рис. 16
Огражденная часть кузовов рефрижераторных вагонов (рис. 16, рис. 17) имеет многослойную термоизоляцию между наружной и внутренней обшивками стен, пола и крыши. По торцам каждого грузового вагона размещены холодильные установки на фреоне-12 в качестве хладагента (в 12-вагонной секции на аммиаке). Вагоны оснащены средствами измерения и контроля температуры воздуха в грузовом помещении. Для обеспечения режимного отопления имеются электропечи. Холодильные установки снабжены приборами автоматики, обеспечивающими управление, регулирование, защиту, контроль работы и сигнализацию без вмешательства человека.
Автономный рефрижераторный вагон АРВ
Рис. 17
Вагон- термос (рис. 18) предназначен для перевозки охлажденных и мороженных СПГ, не выделяющих биологического тепла. Кузов такого вагона имеет конструкцию типа «сэндвич» с изоляцией из твердого пенистого полиуретана. Вагон может эксплуатироваться при температуре наружного воздуха от –50 до +50°С. Допускаемый срок перевозки зависит от температуры груза перед погрузкой и допускаемой конечной при выгрузке, а также температуры наружного воздуха. Кузов вагона цельнометаллический. Наружная обшивка его выполнена из низколегированной стали, а внутренняя — из алюминиевого сплава. Потолок кузова обшит экоталью толщиной 0,75 мм. Экоталь представляет собой оцинкованный стальной лист, покрытый со стороны грузового помещения жаропрочной пленкой из пластмассы или слоем специального лака. Боковые стены имеют вертикальные гофры. В торцах грузового помещения установлены защитные стенки из оцинкованного листа для предотвращения повреждения основной торцовой стены при сдвиге груза. Пол состоит из двух слоев стеклопластика, между которыми находятся бумажные вертикальные сегменты, (соты), заполненные вспененным полиуретаном. На верхний слой стеклопластика наложена многослойная фанера толщиной 18 мм, которая покрыта биологически нейтральной резиной. В грузовом помещении расположены оцинкованные стальные напольные решетки. В полу по диагонали на обоих конах вагона предусмотрены два устройства для удаления промывочных вод.
Вагон-термос
Рис. 18
Порядок выполнения и оформления работы.
Записать название и цель работы, заполнить табл. 9
Таблица 9
Параметры грузовых вагонов
Назначение вагона | Грузоподъемность, т | Тара, т | Габарит подвижного состава | Материал кузова | Тип автосцепки | Тип тележки |
Ответить на контрольные вопросы
7.2.1. Перечислить основные типы вагонов грузового парка.
7.2.2. Определить назначение и виды вагонов промышленного парка.
7.2.3. Описать вагоны для перевозки жидких грузов.
7.2.4. Определить назначение изотермических вагонов.
7.2.5. Перечислить преимущества контейнерных перевозок.
7.3. Записать выводы по выполненной работе.
ЛАБОРАТОРНАЯ РАБОТА № 3
studfiles.net